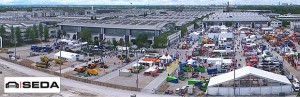
Anniversary IFAT sets new benchmark
Around 138,000 visitors from over 170 countries came to Munich for the anniversary edition of IFAT between May 30 to June 3, 2016. A total of 3,097 exhibitors—1,695 companies from Germany and 1,402 from around the world—coming from 59 countries, presented their innovations and new developments for the environmental technology sector on 230,000 square meters of exhibition space.
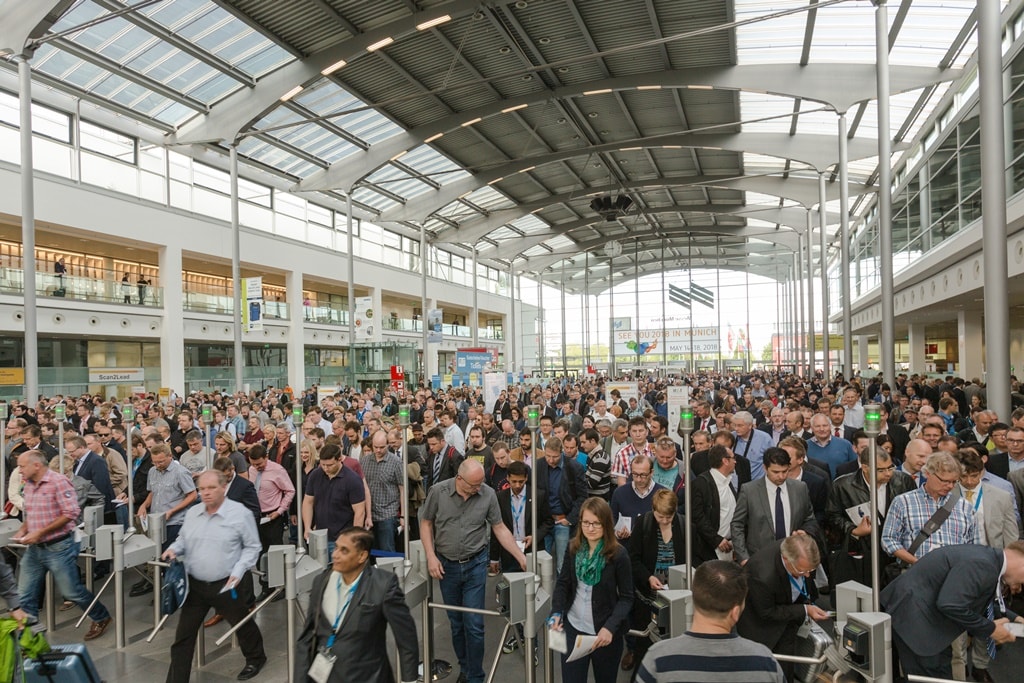
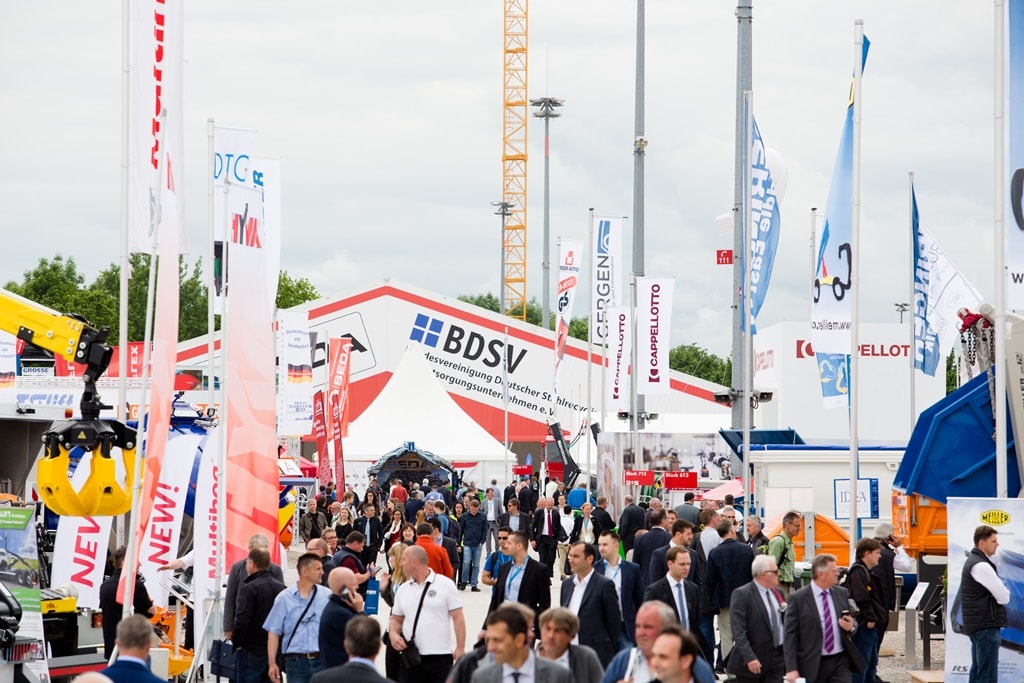
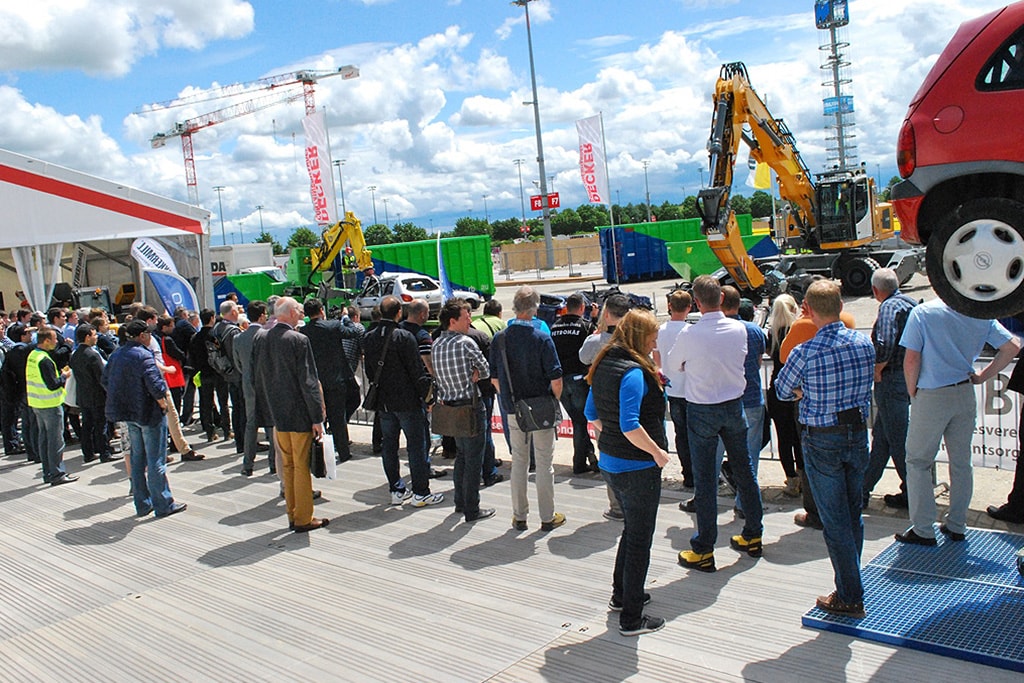
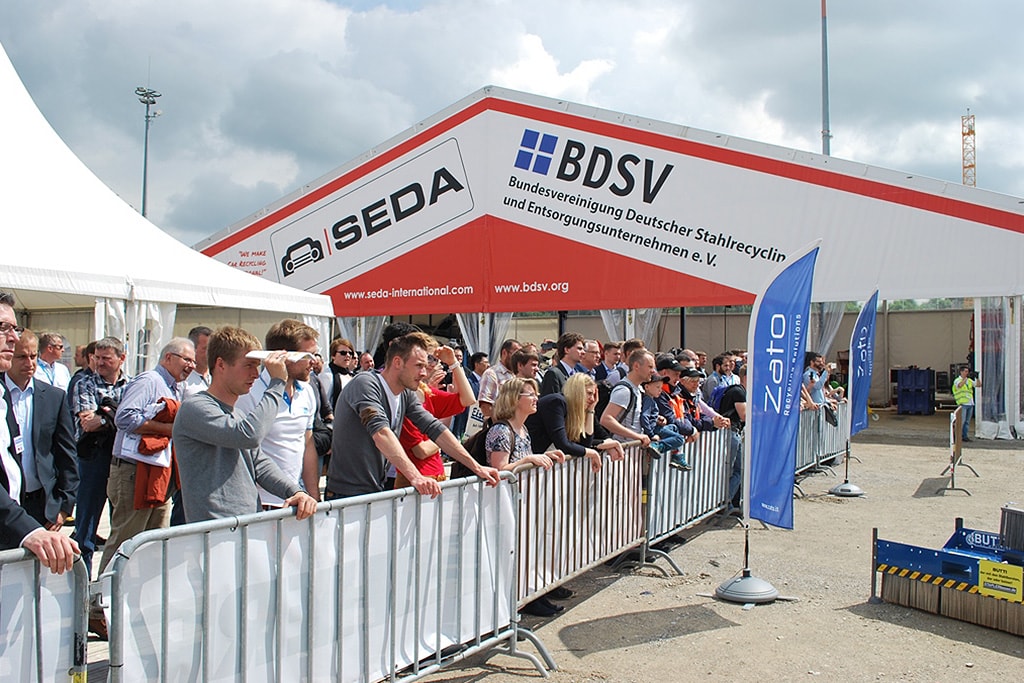
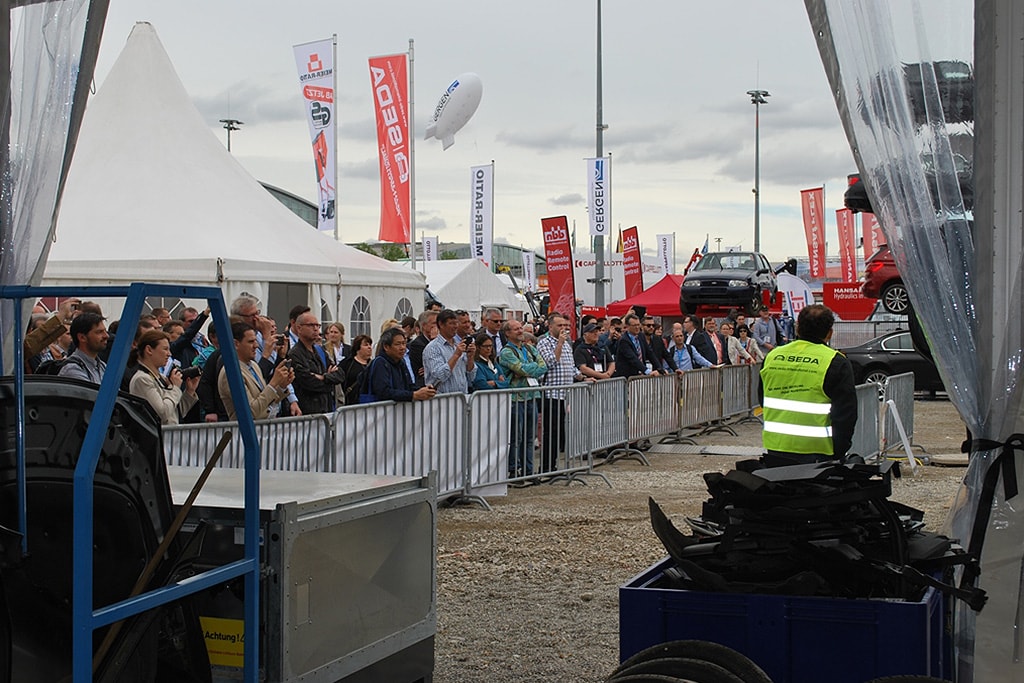
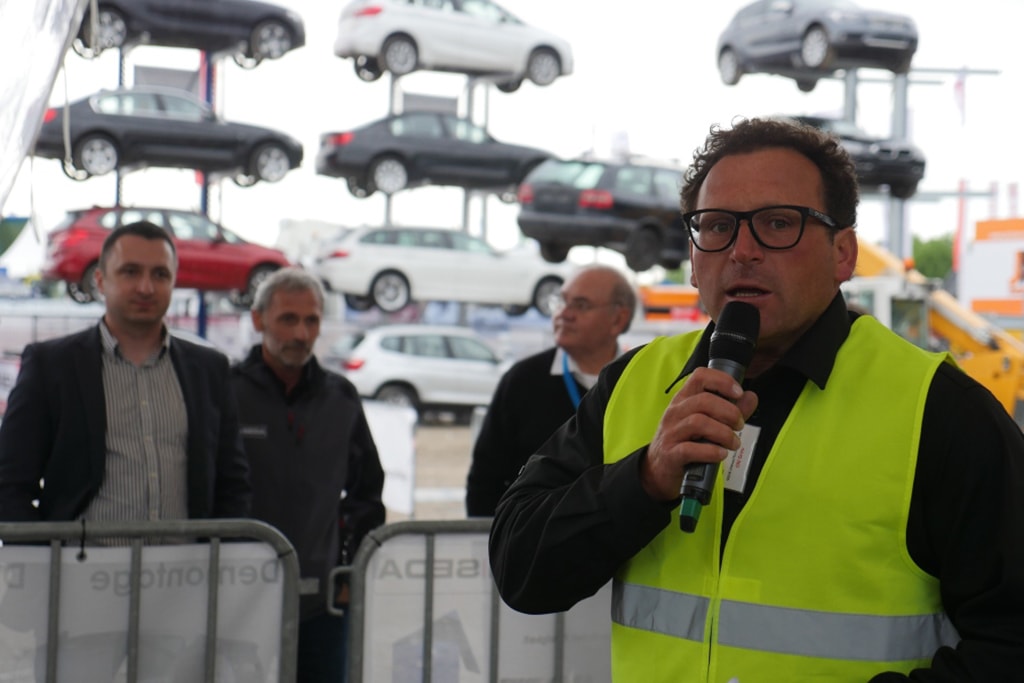
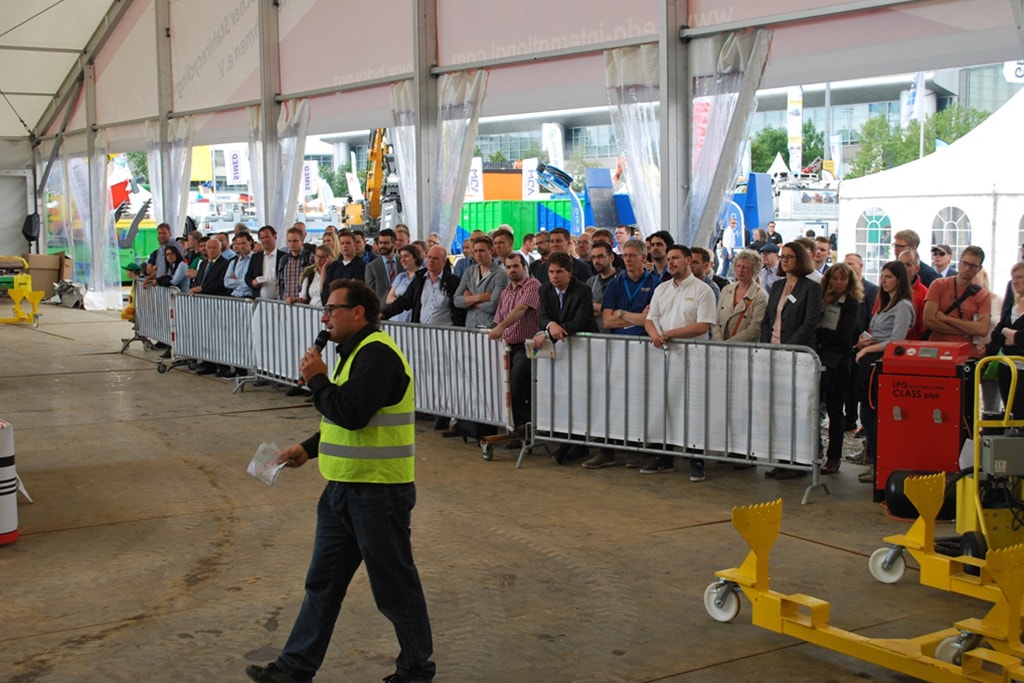
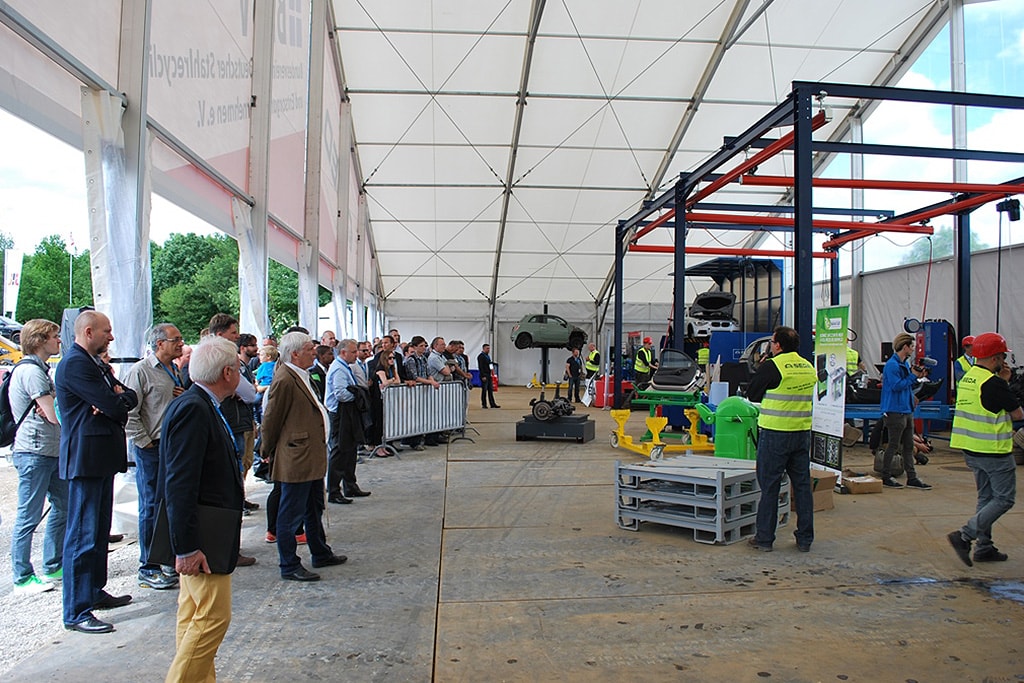

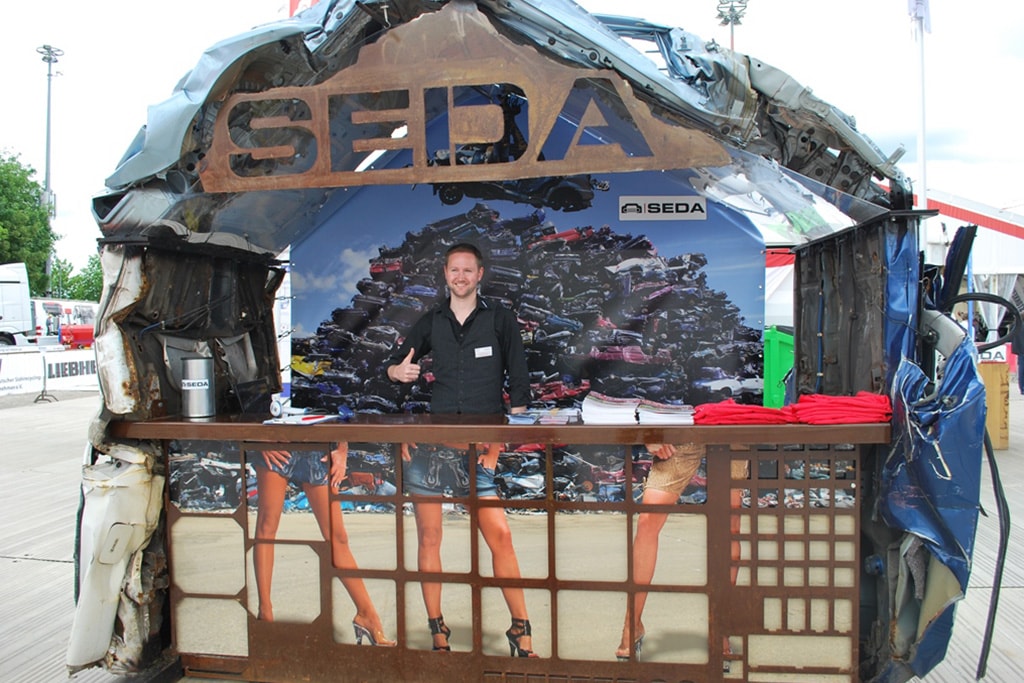
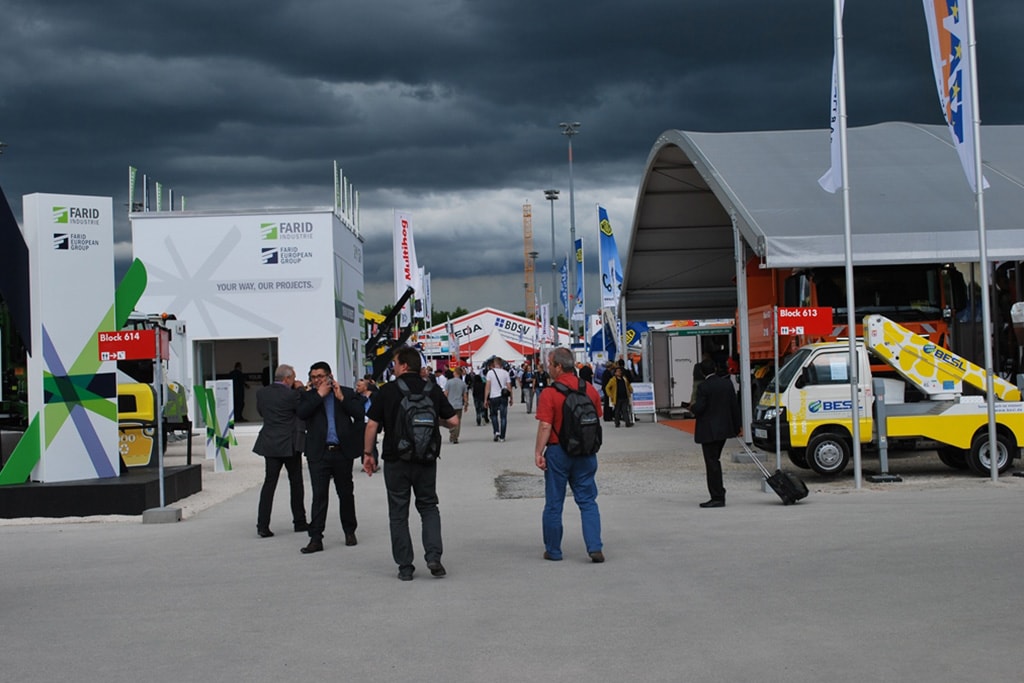
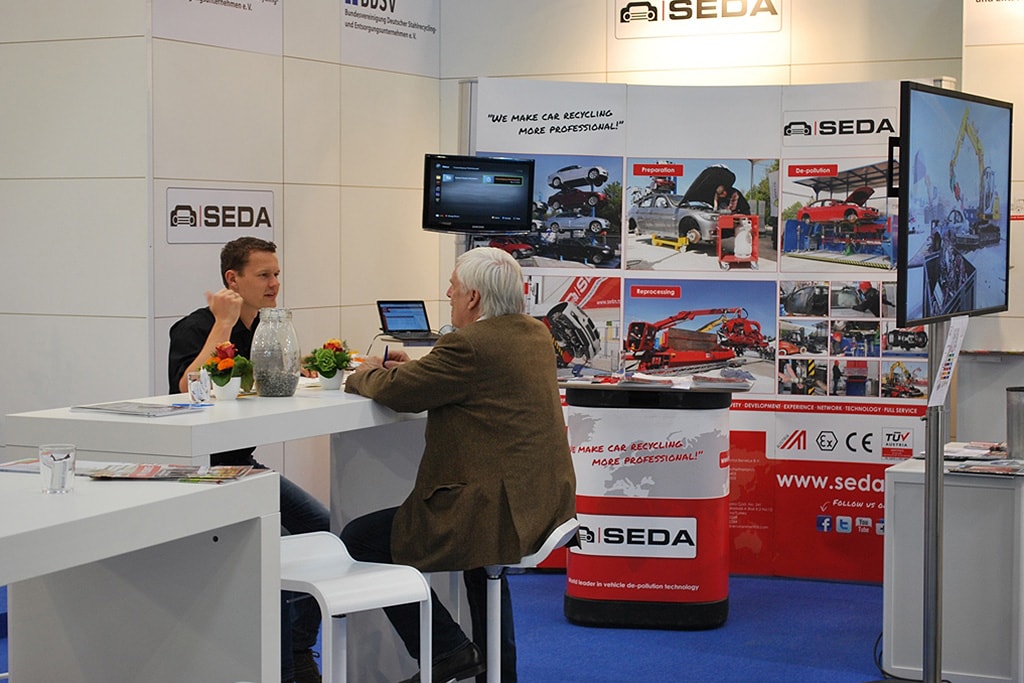
IFAT car recycling video
Car recycling steps
The complete process is divided into the following stations:
- Storage
- Preparation
- De-pollution
- Dismantling
- Reprocessing
- Compression
01 Storage
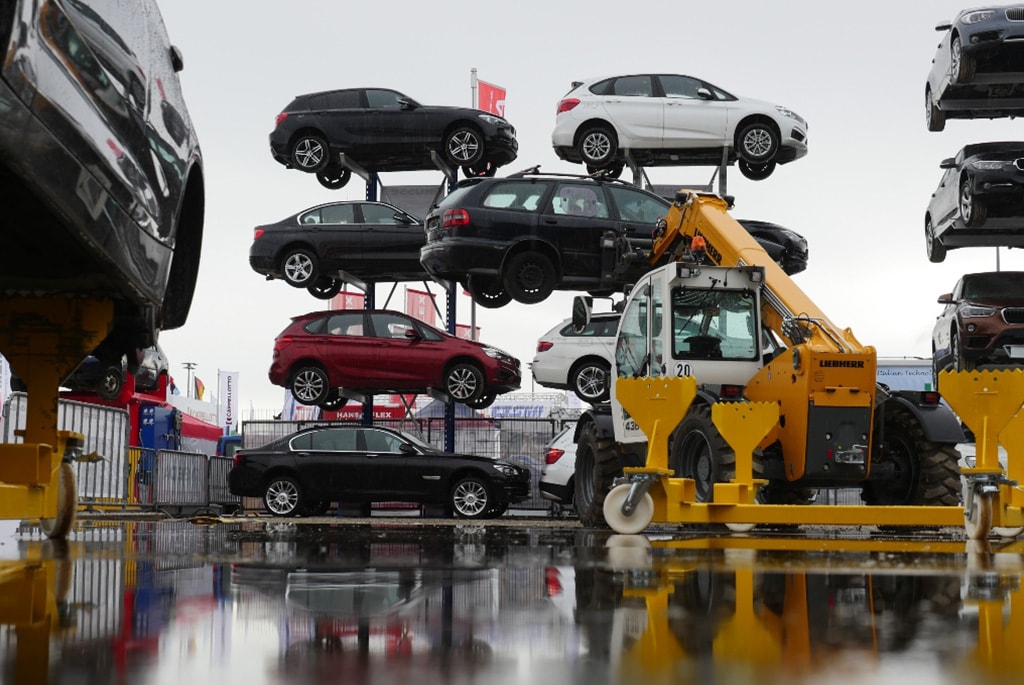
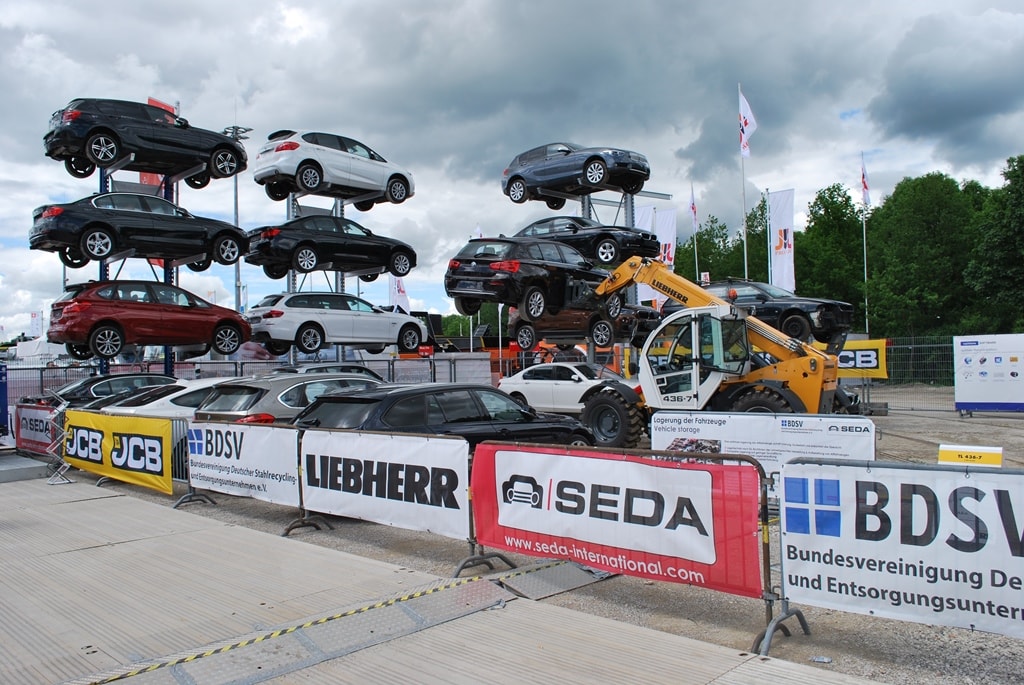
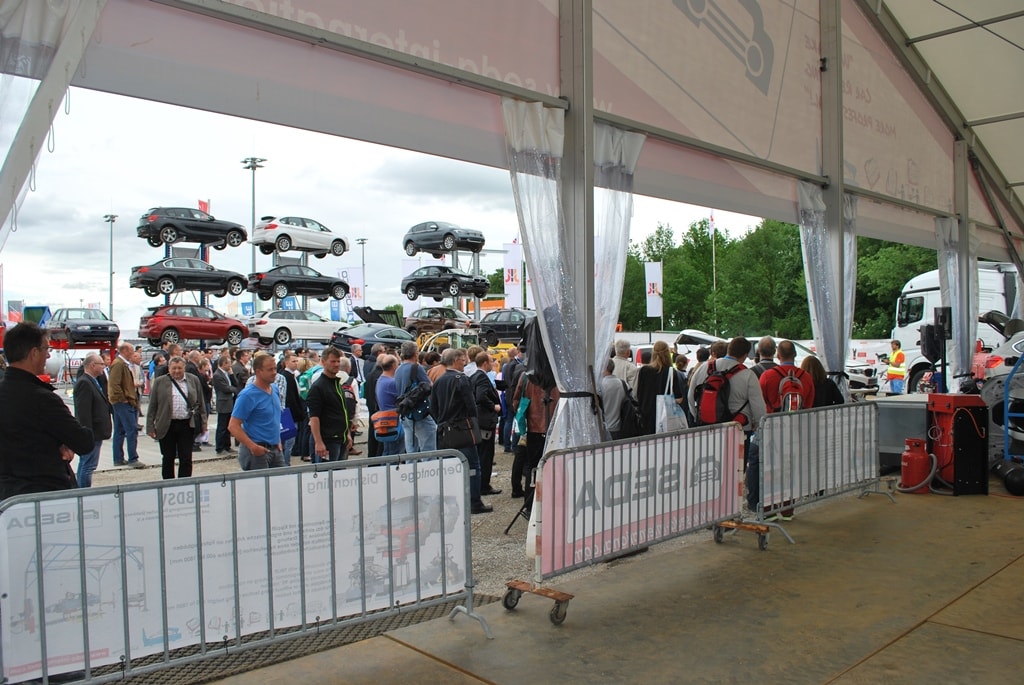
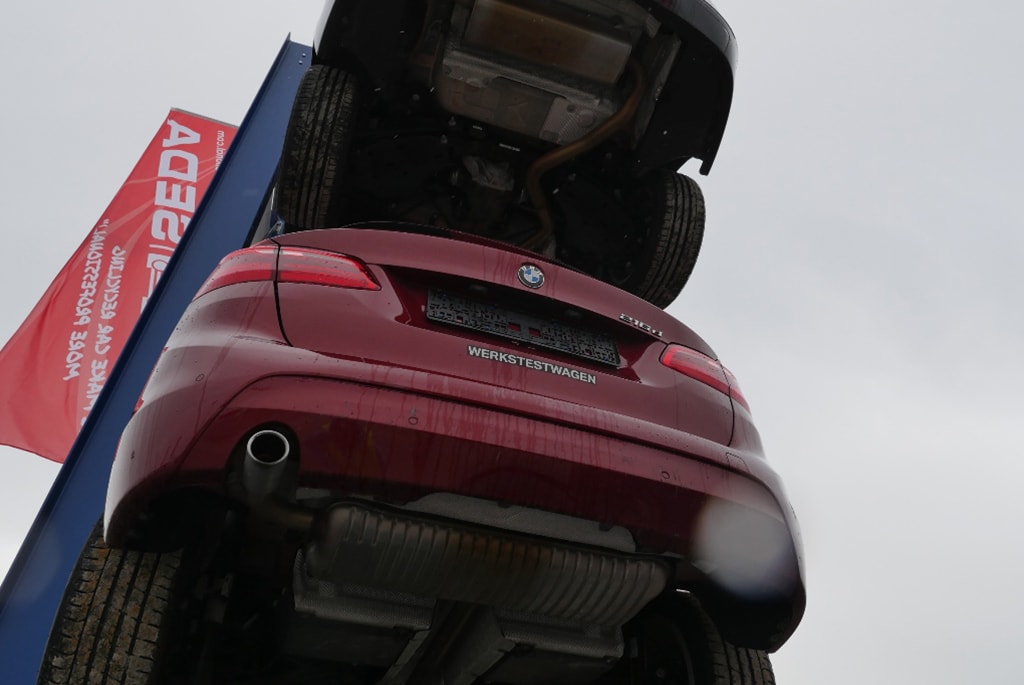
At the first station you can see the perfect storage solution for vehicles. A compact storage of ELVs on a small footprint according to EU directives helps to guarantee order and cleanliness. A computerized warehouse management system allows a direct access to each individual vehicle.
02 Preparation
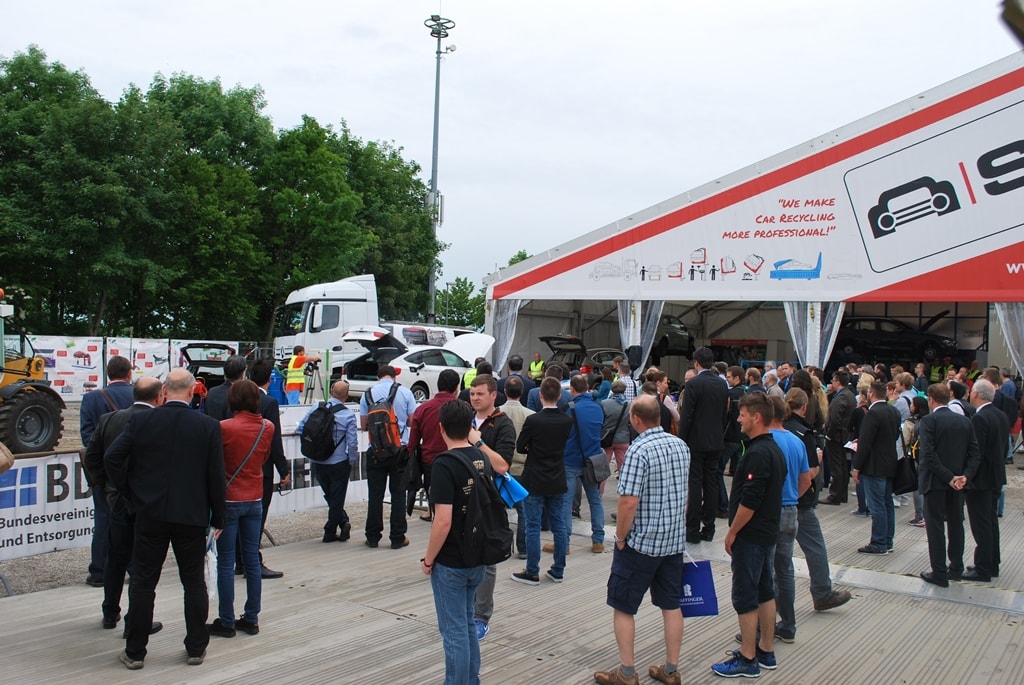
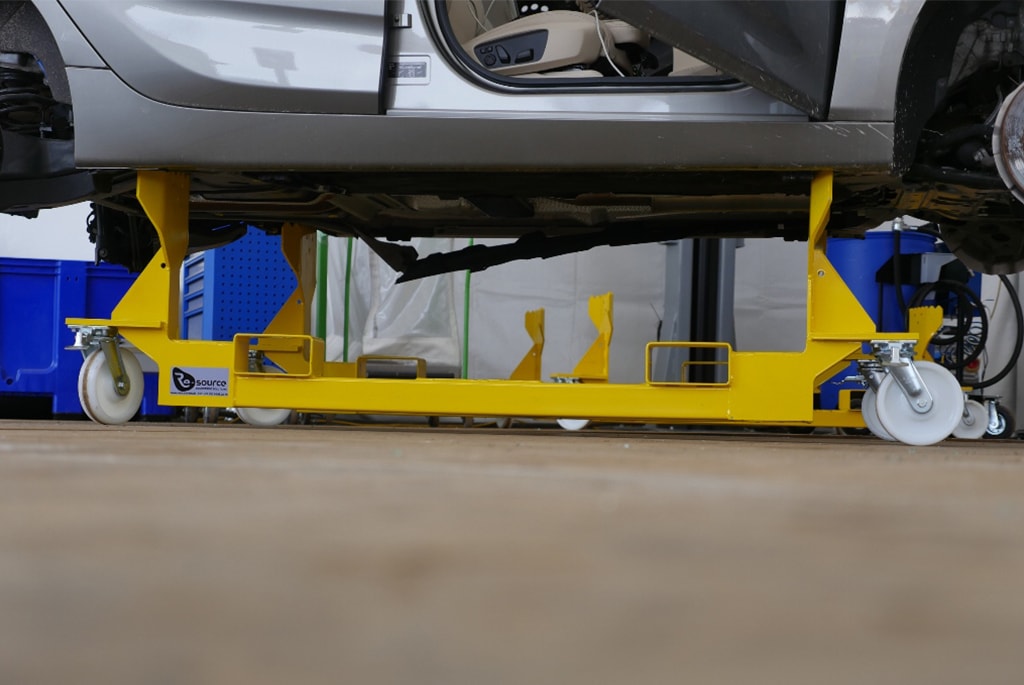
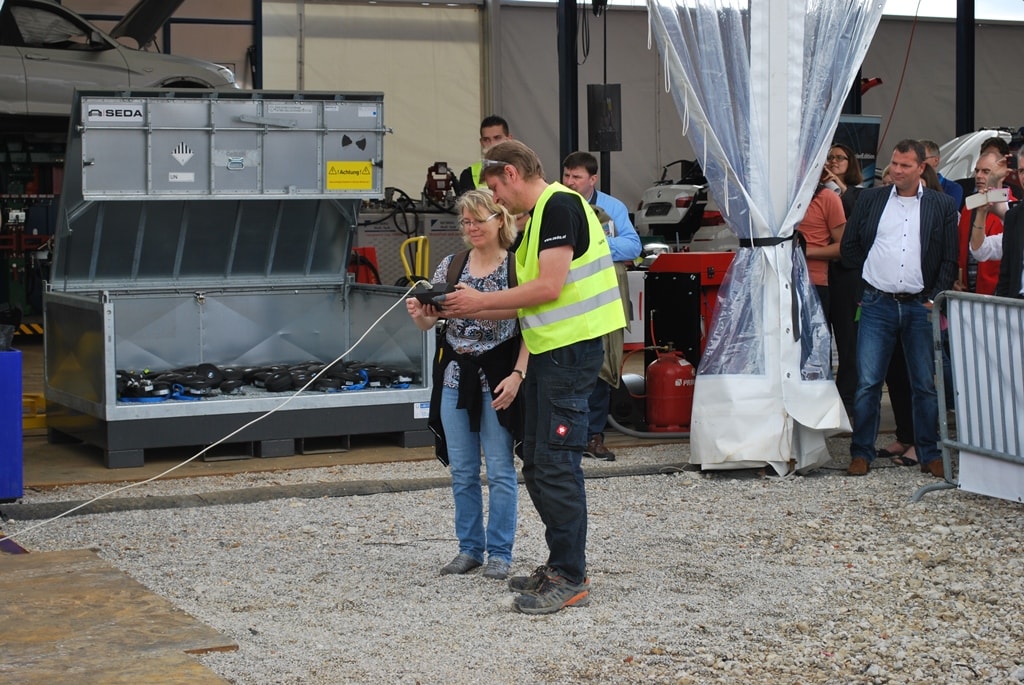
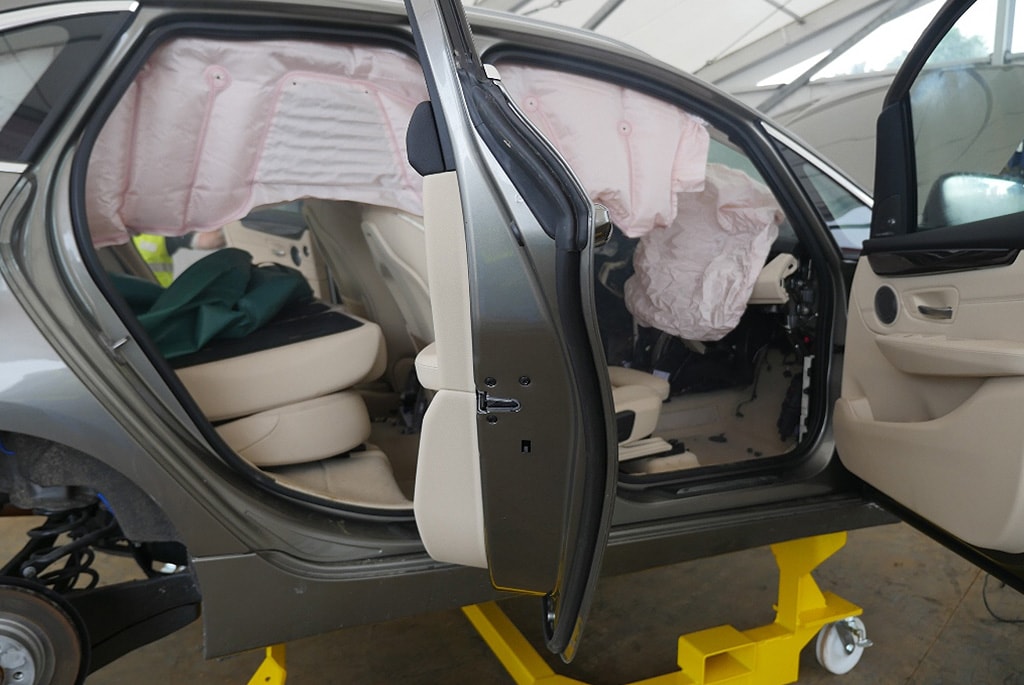
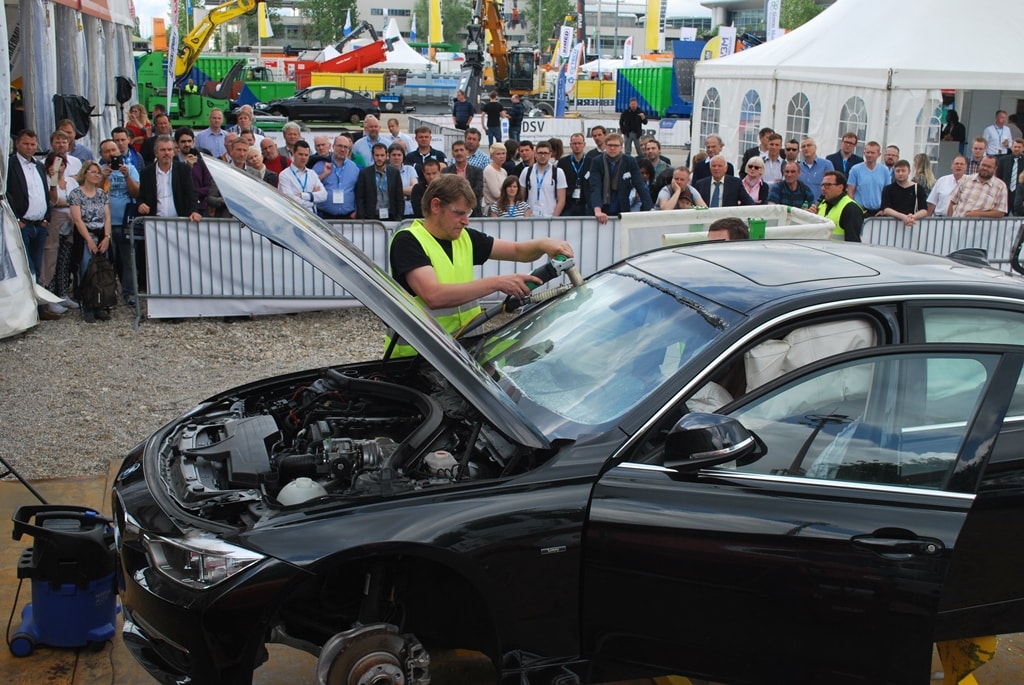
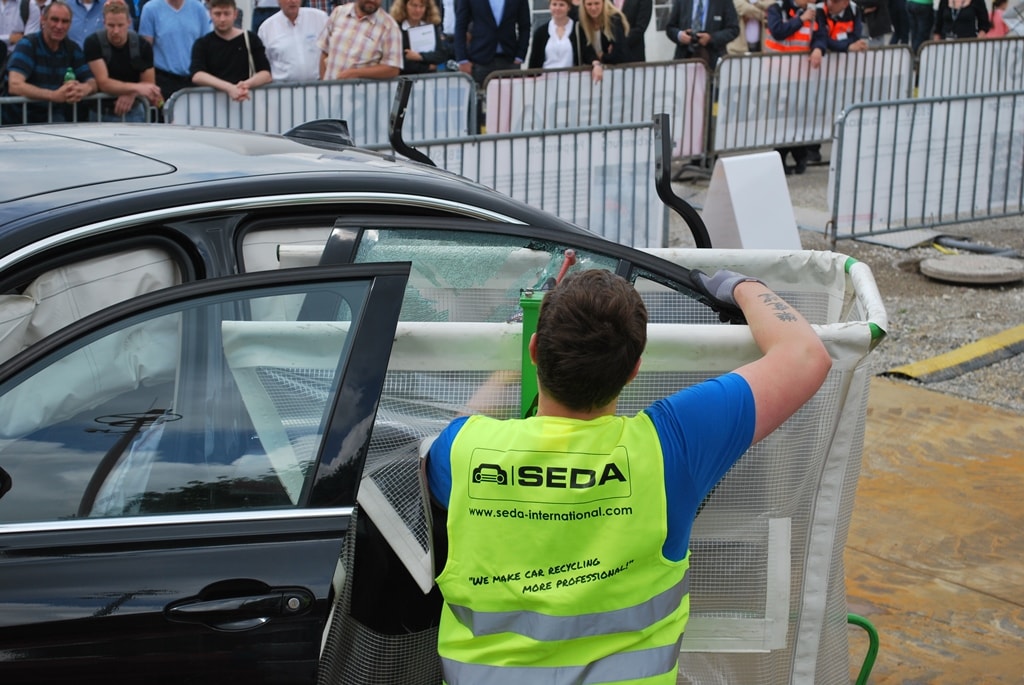
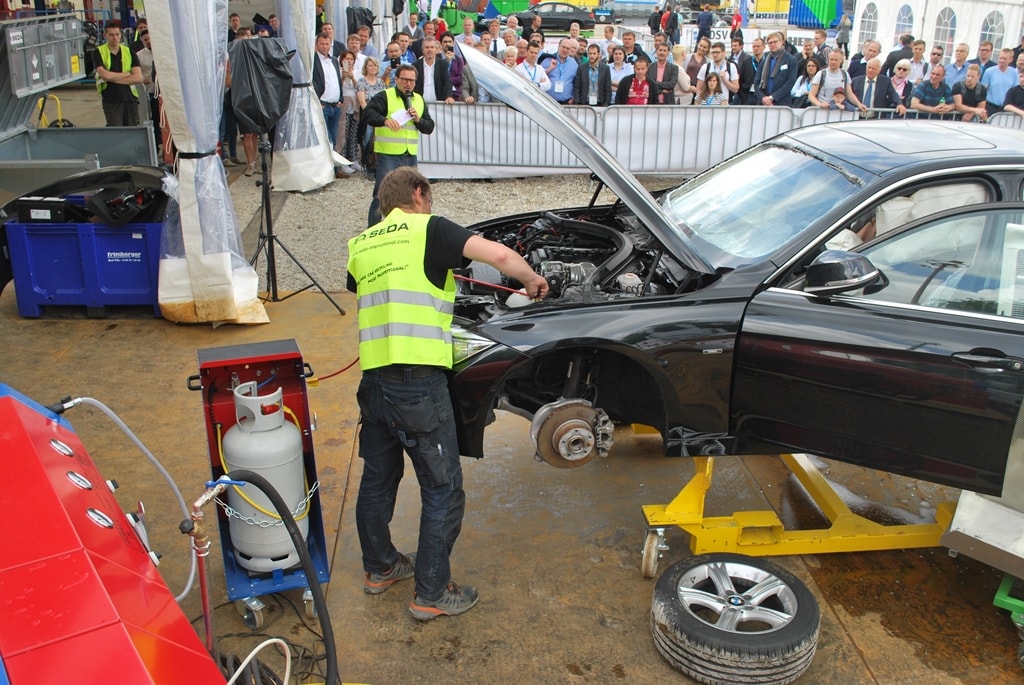
The second station includes the preparation of ELVs for an efficient processing. At first, the vehicle is placed on a trolley for a forklift-free use. Vehicle registration is recorded with the help of a computer software. After that battery and tyres are removed as well as air-conditioning gas. Finally pyrotechnic safety devices like airbags and belt tensioners are deployed and the glass is removed.
03 De-pollution
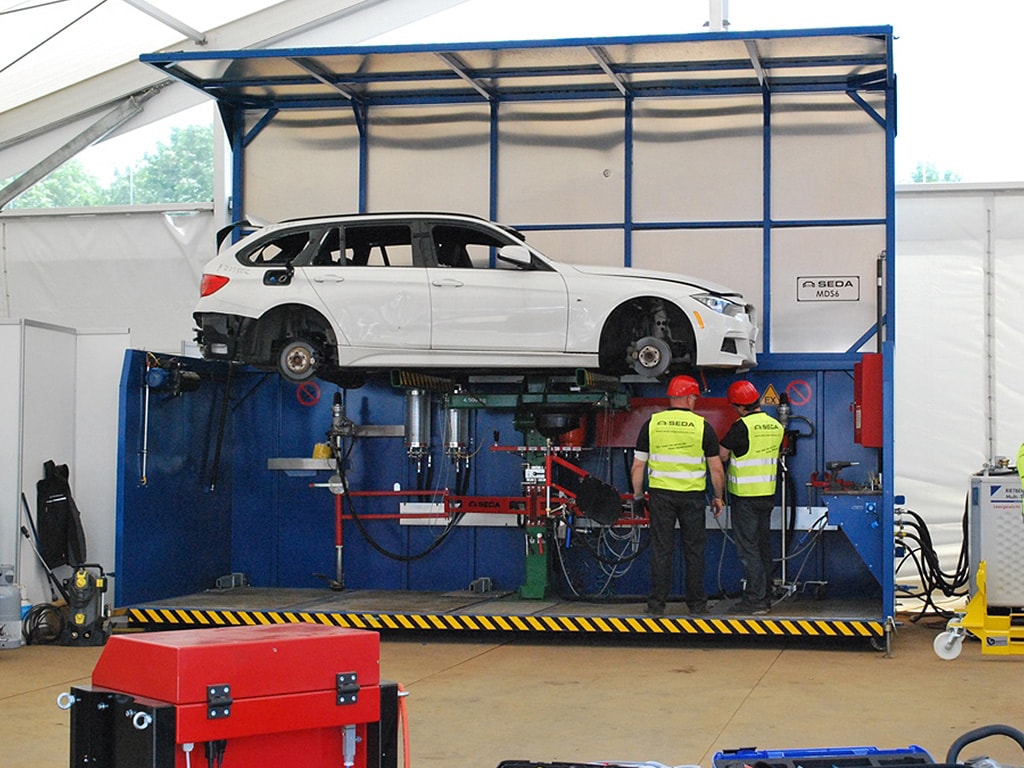
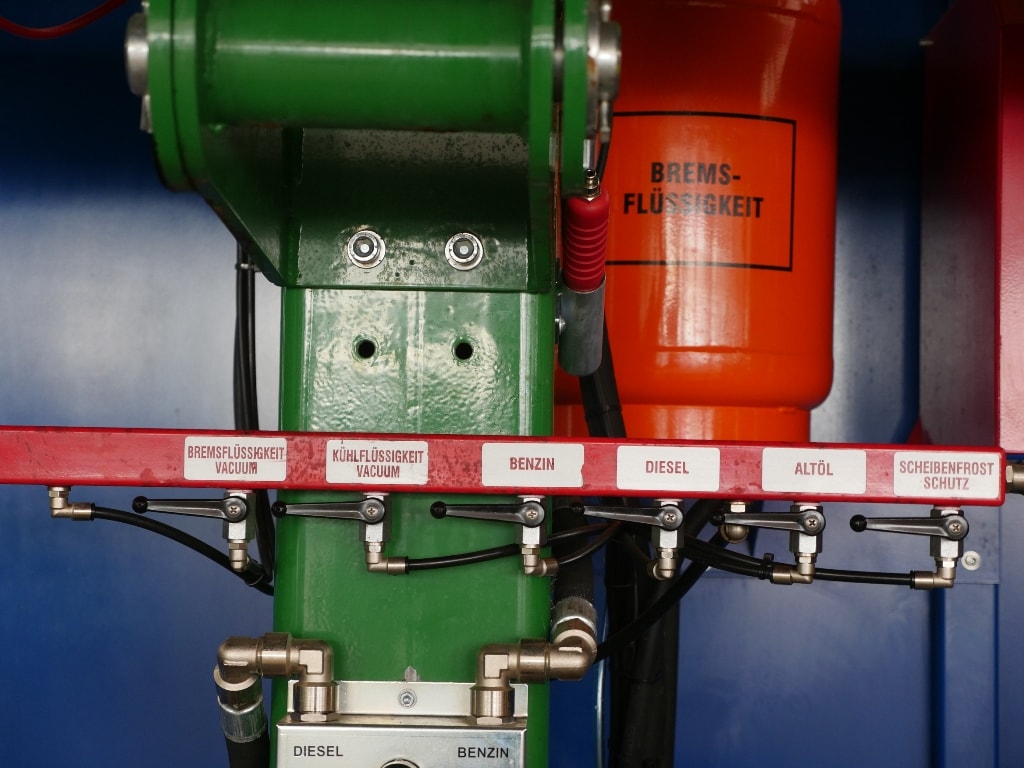
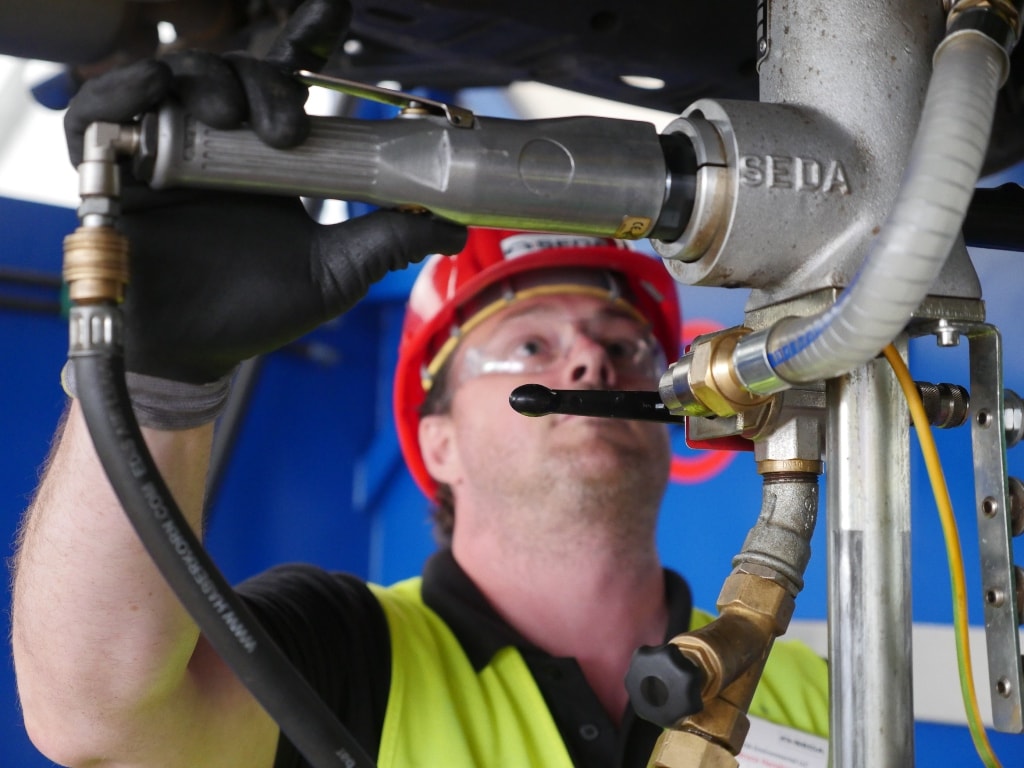
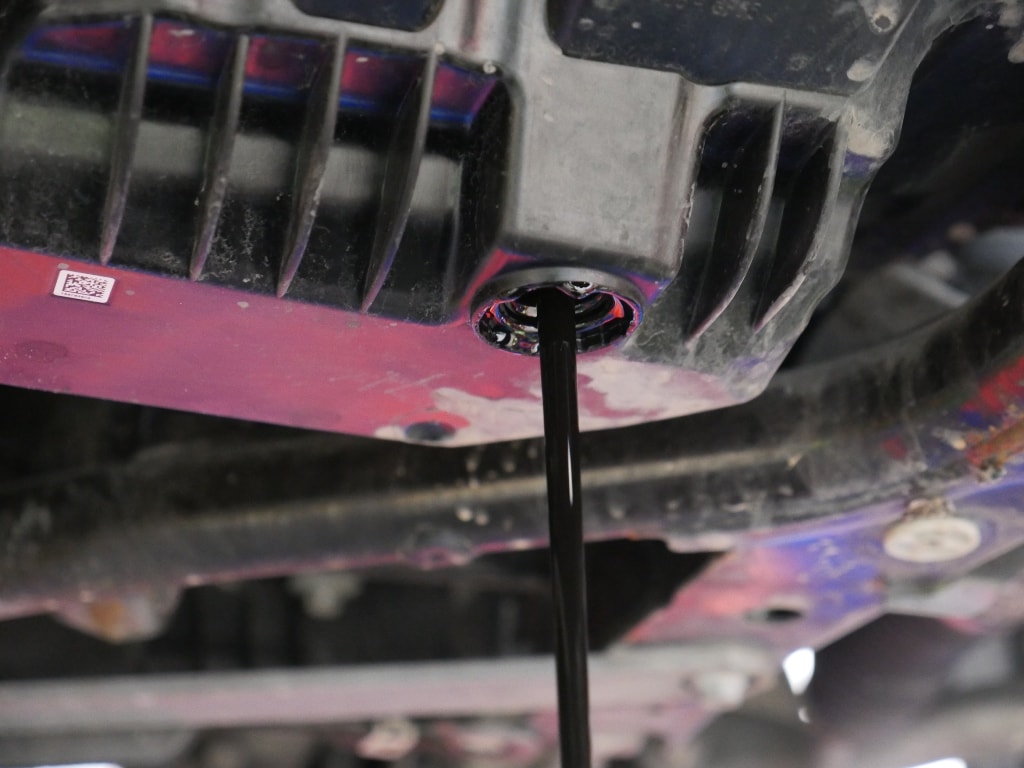
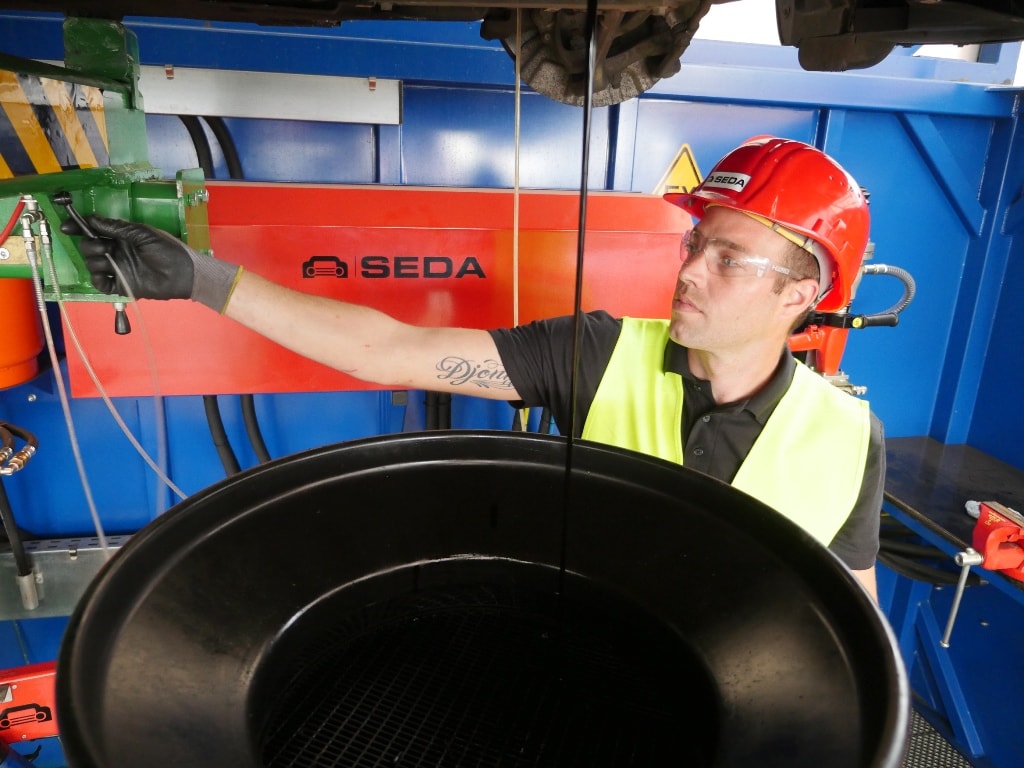
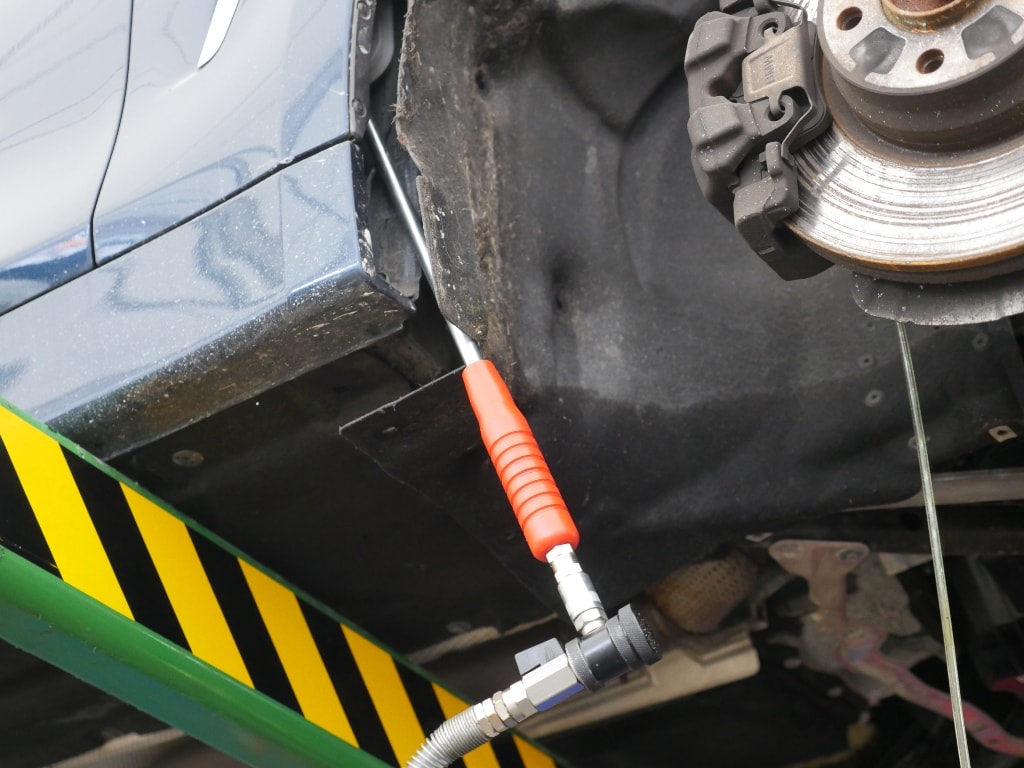
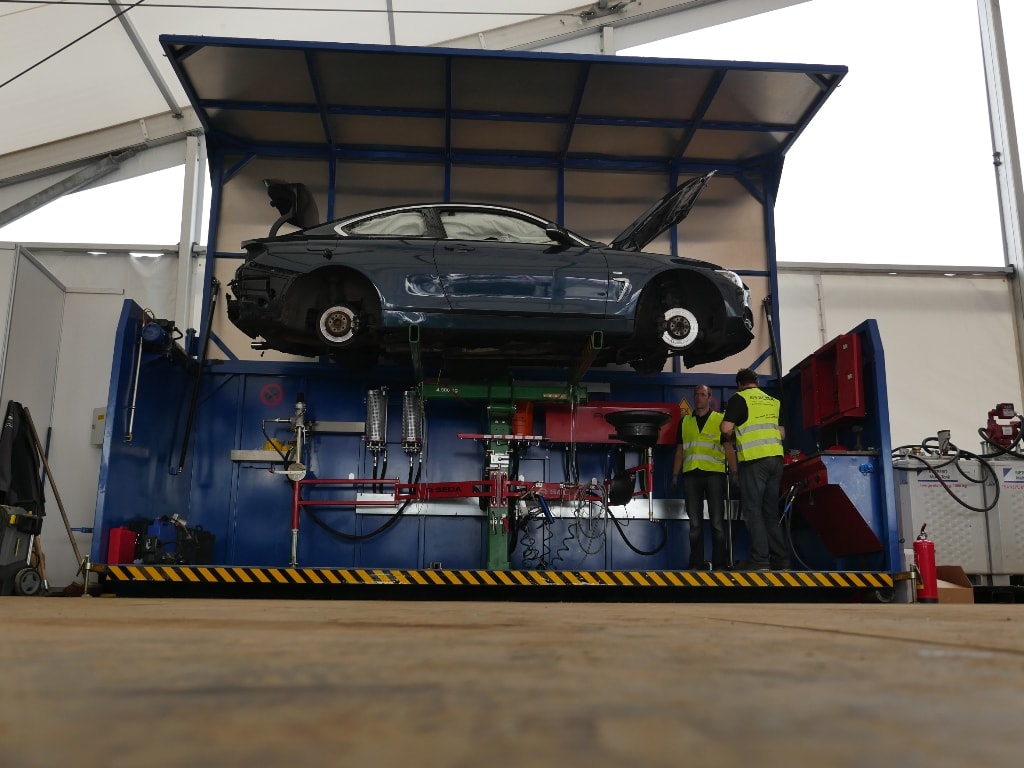
The third step is de-pollution which takes place at SEDA’s MDS6 container. This plug-in and play solution fulfills the highest EU directive standards. On average, an ELV contains 22 liters of harzardous liquids like petrol/diesel, coolant, brake fluid, engine oils, transmission oils, hydraulic oils and windshield washer fluid. With the help of SEDA equipment these liquids can be removed efficiently and completely secure.
04 Dismantling
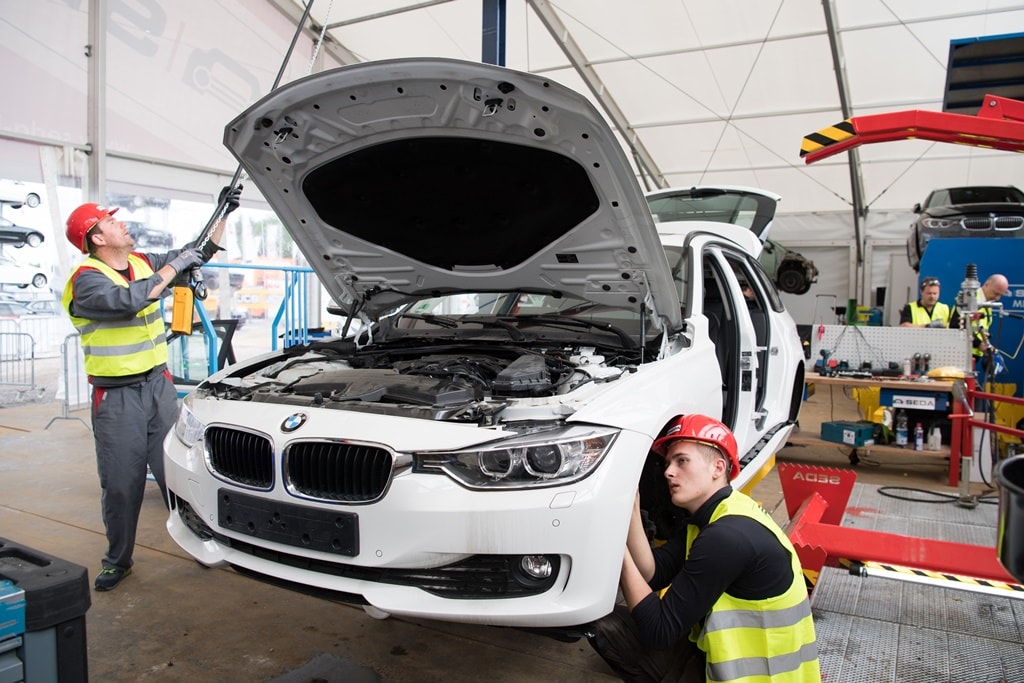
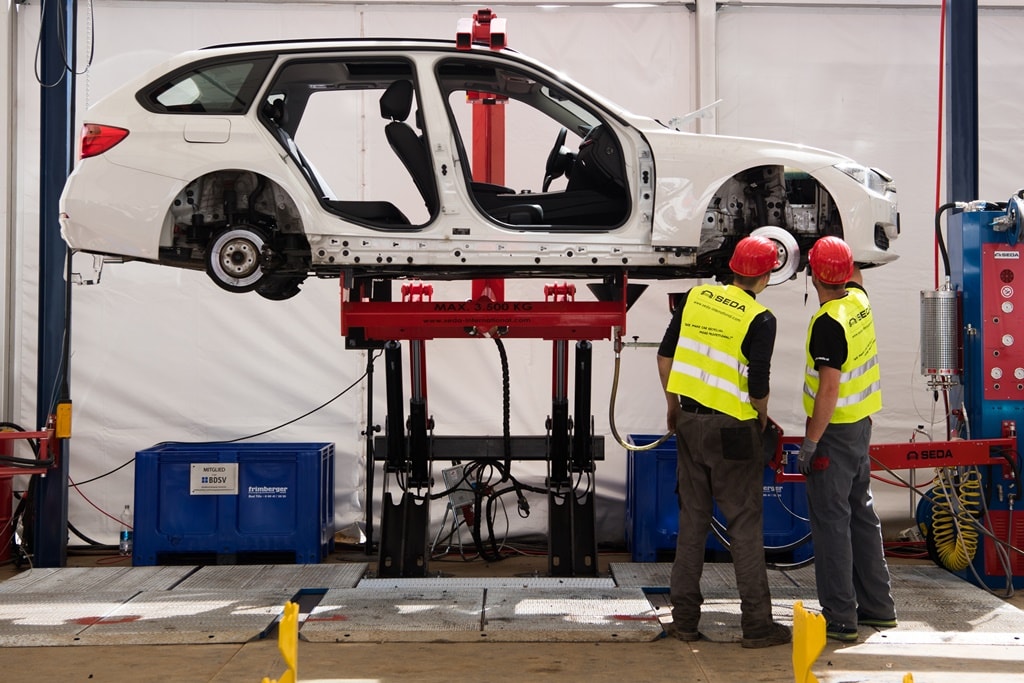
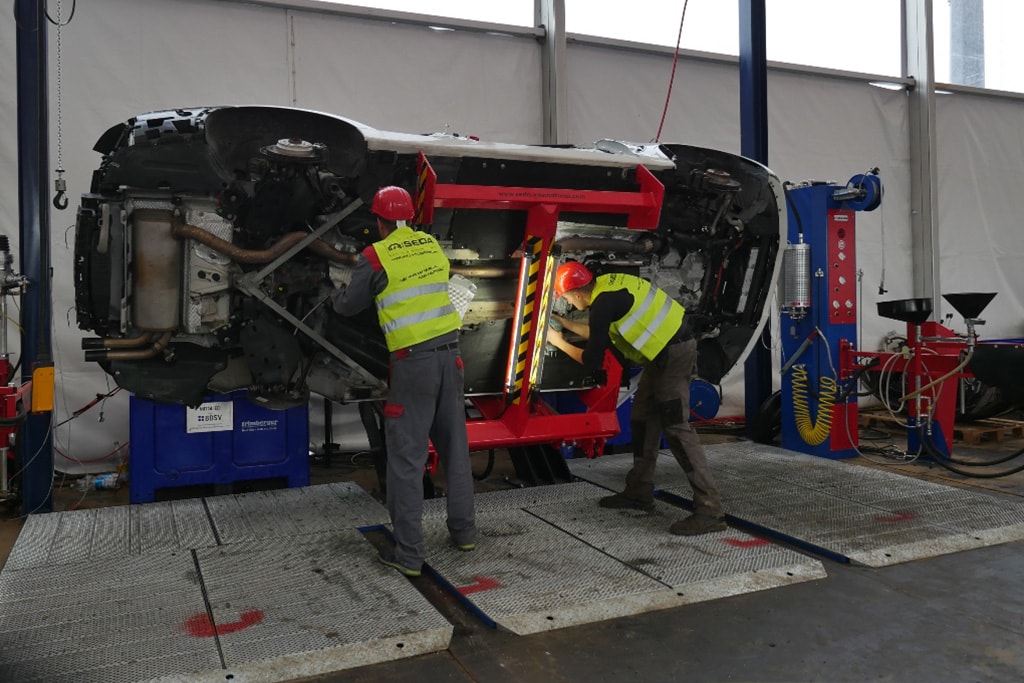
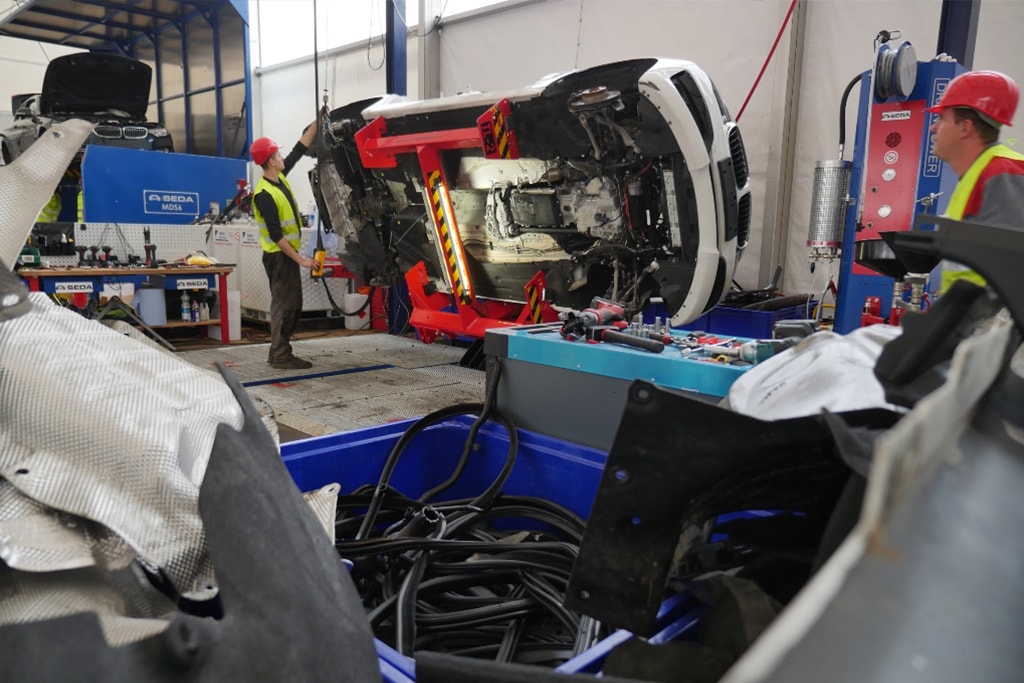
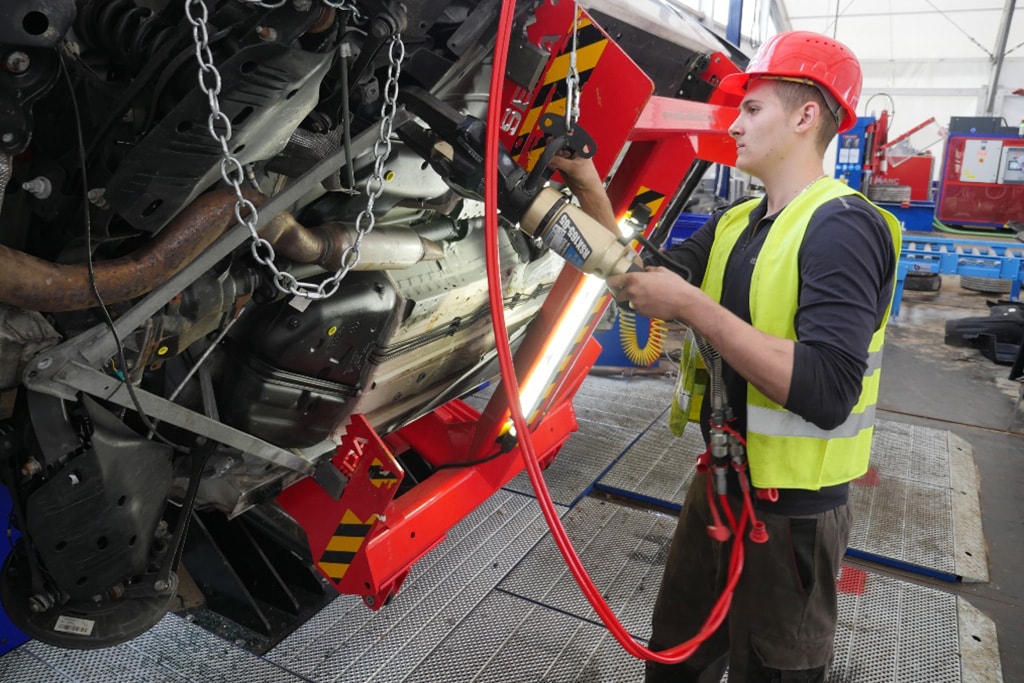

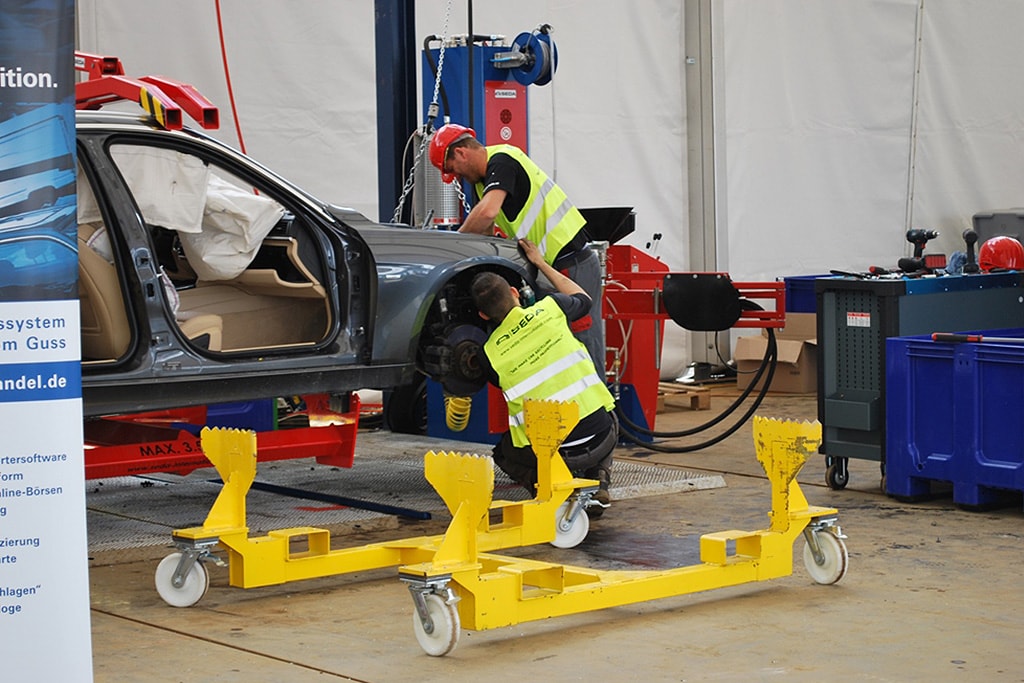
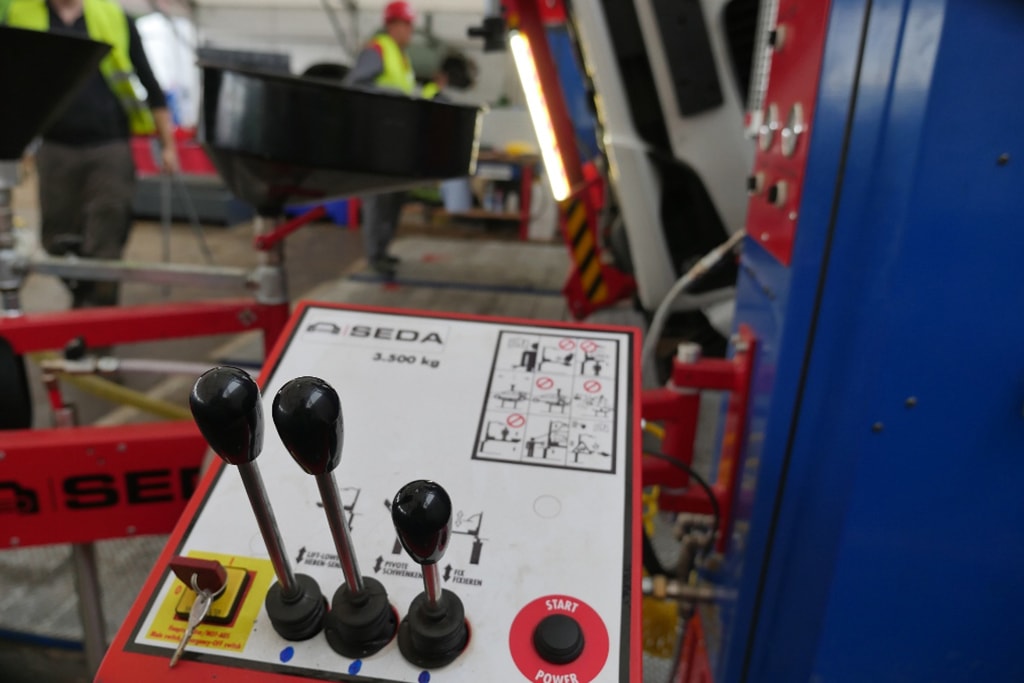
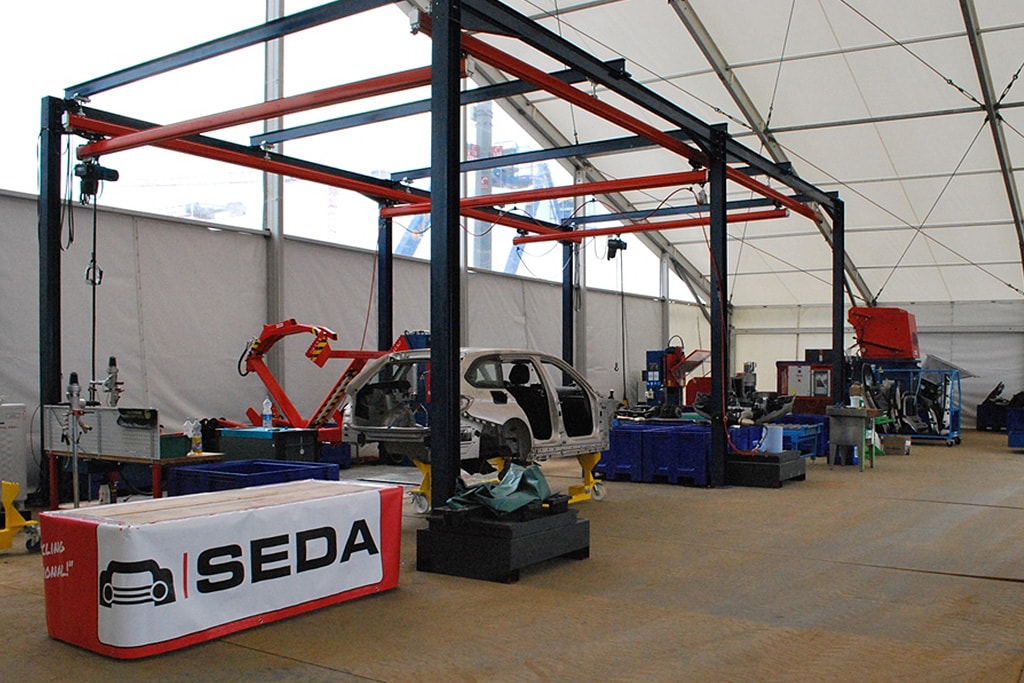
Station number 4 shows the dismantling of a cars by using the SEDA All-In-One Solution. Parts removal and de-pollution in one place – that’s revolutionary and makes this SEDA system unique. A special TiltingLift guarantees a simple and ergonomic work with its multi positioning. You move the car – not the worker. It’s possible to de-pollute and dismantle a complete ELV within 2 – 3 hours.
05 Reprocessing
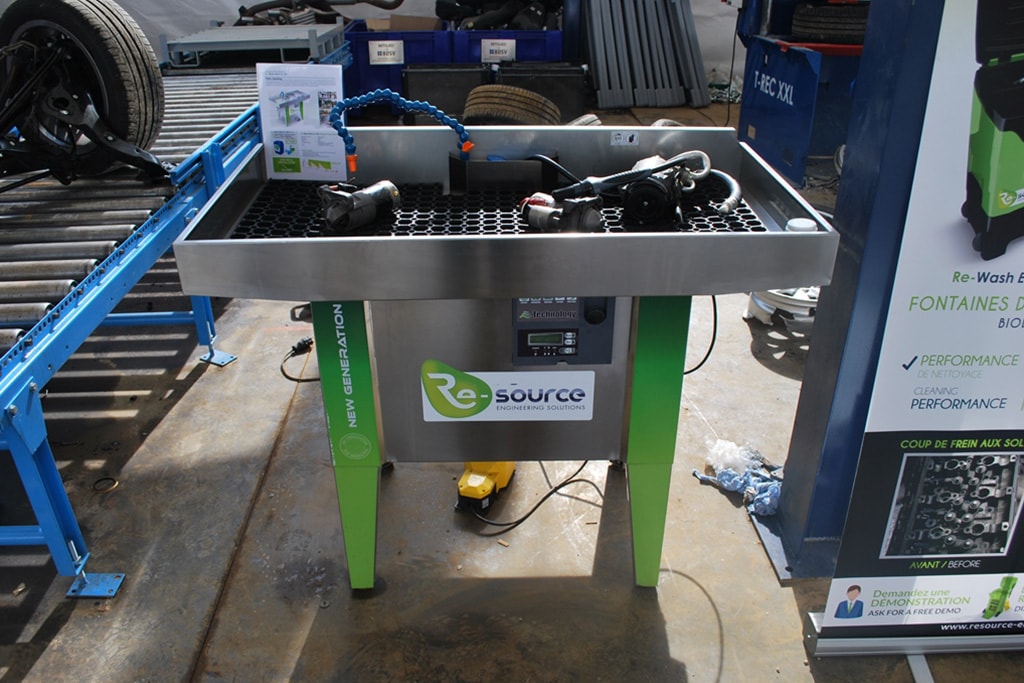
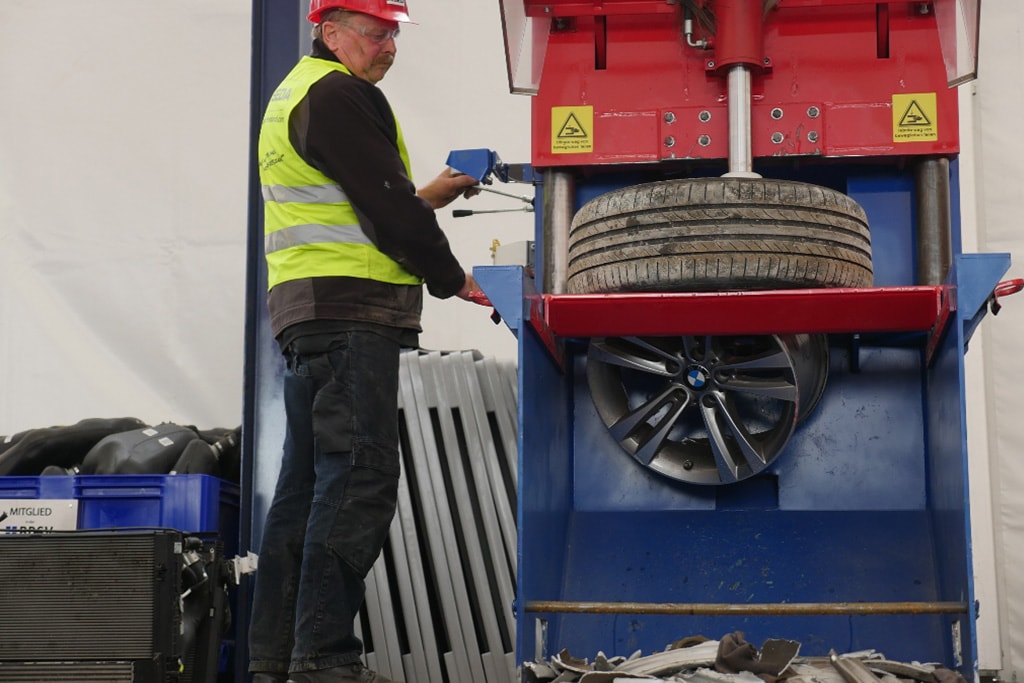
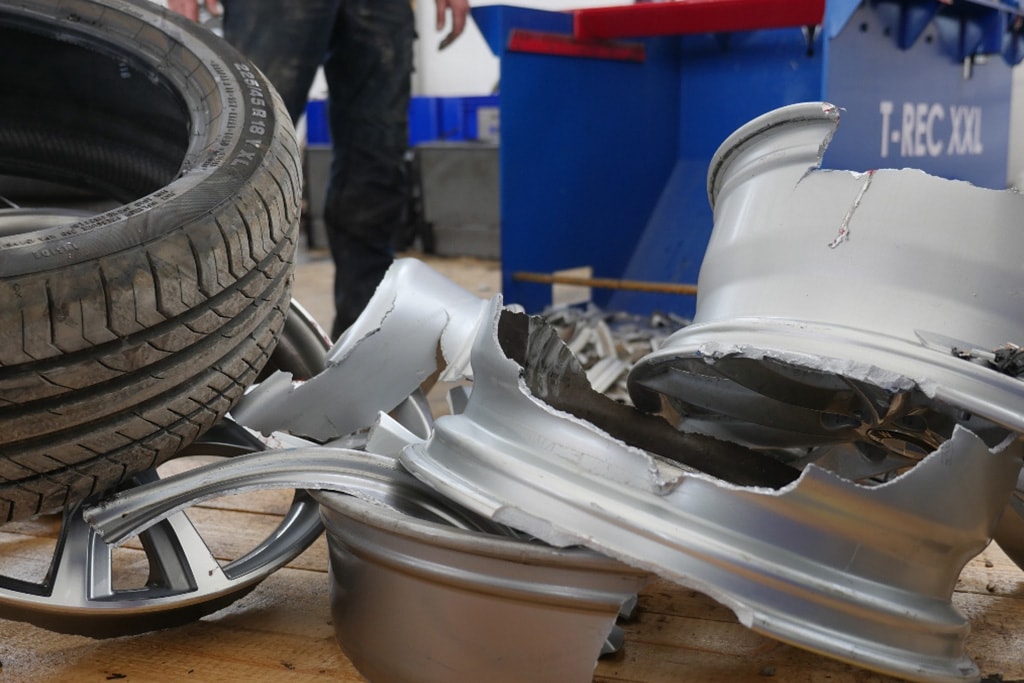
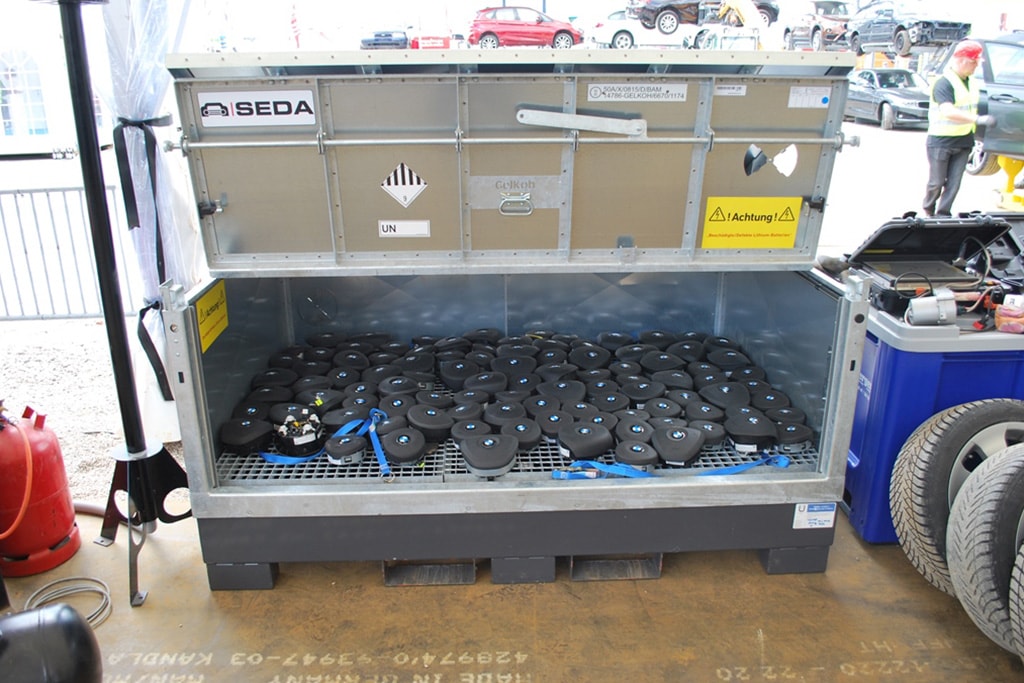
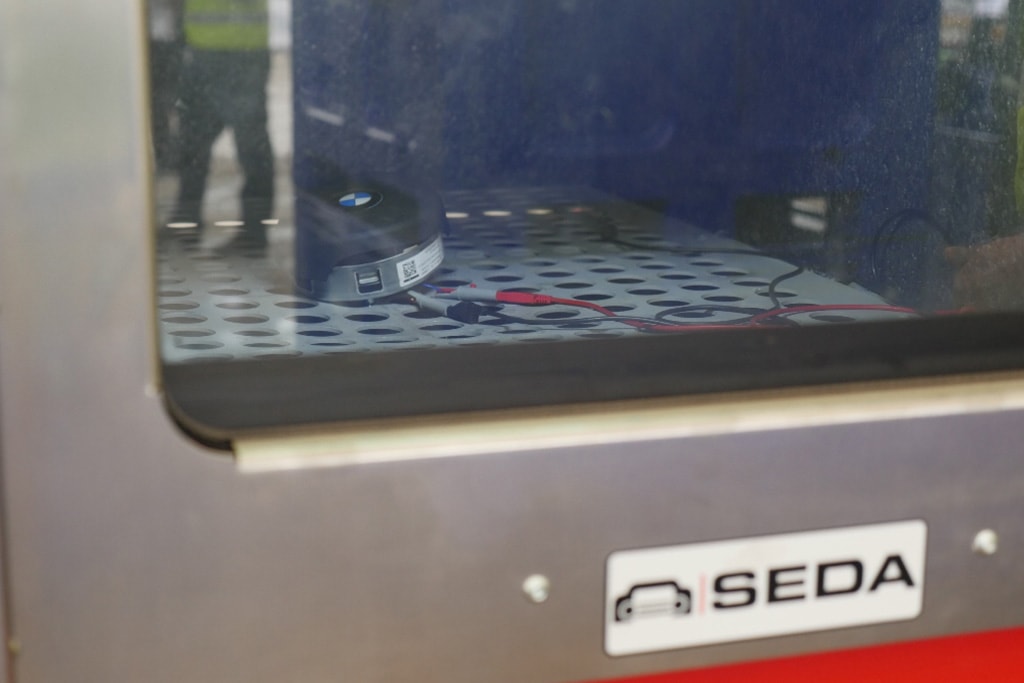
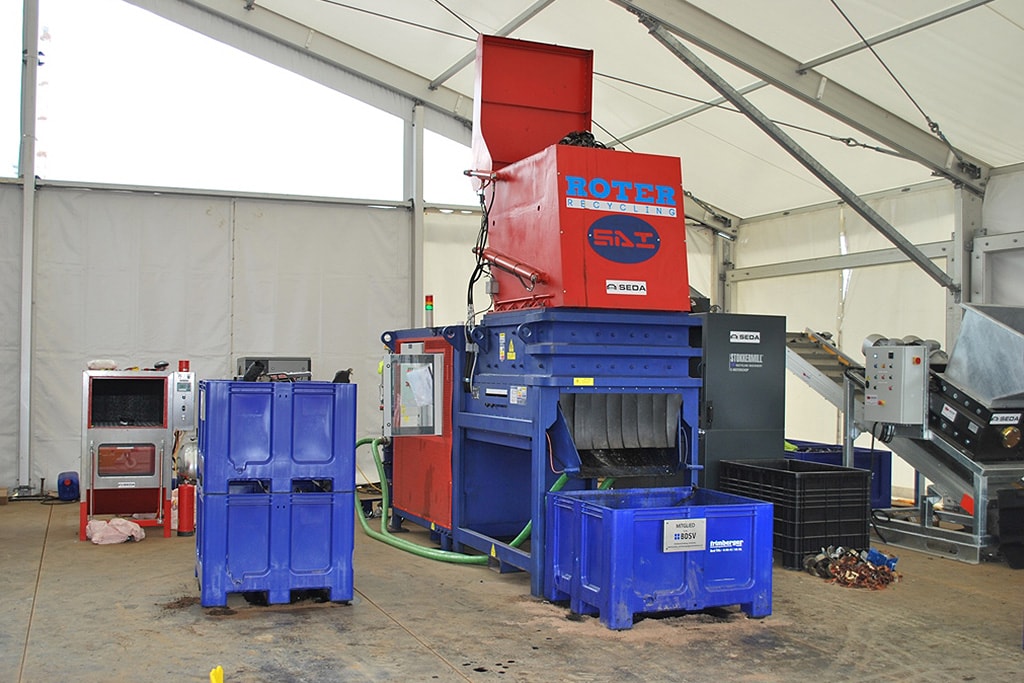

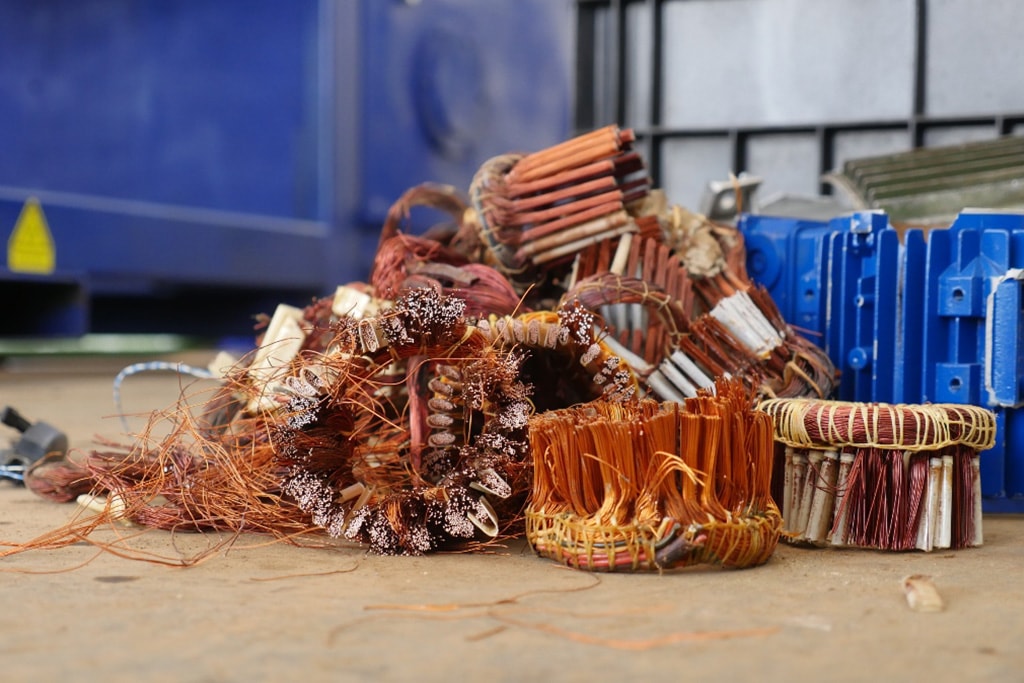
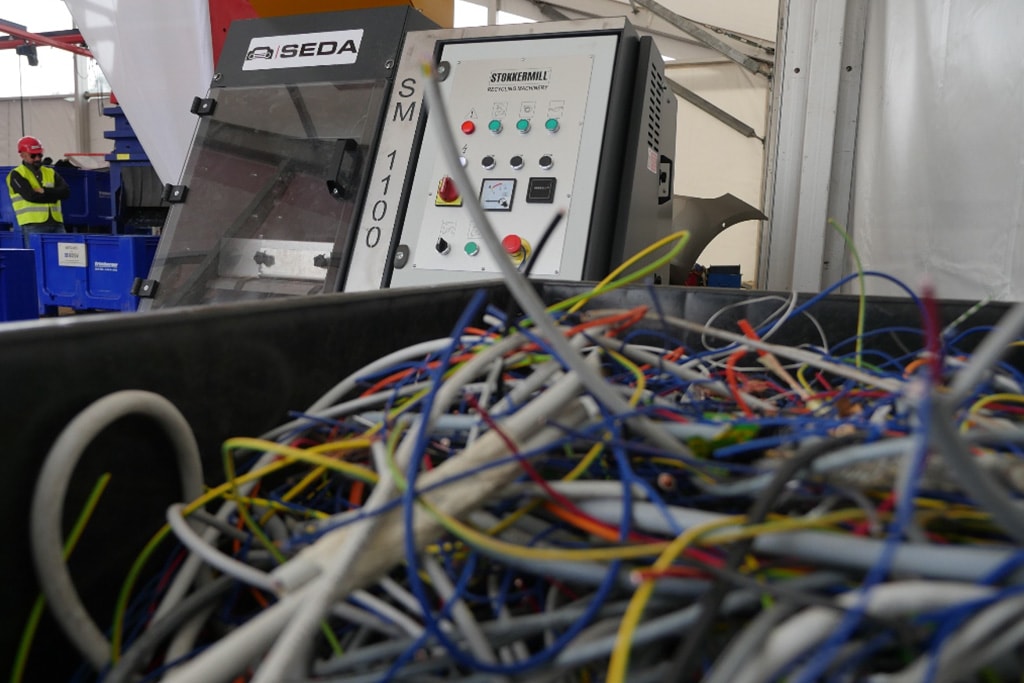
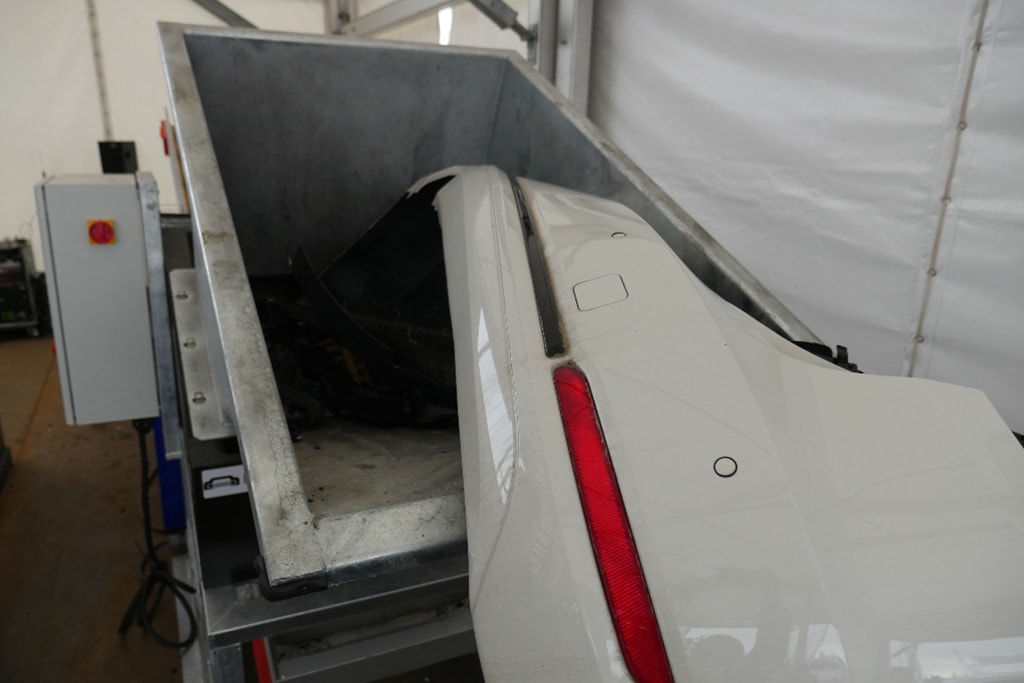
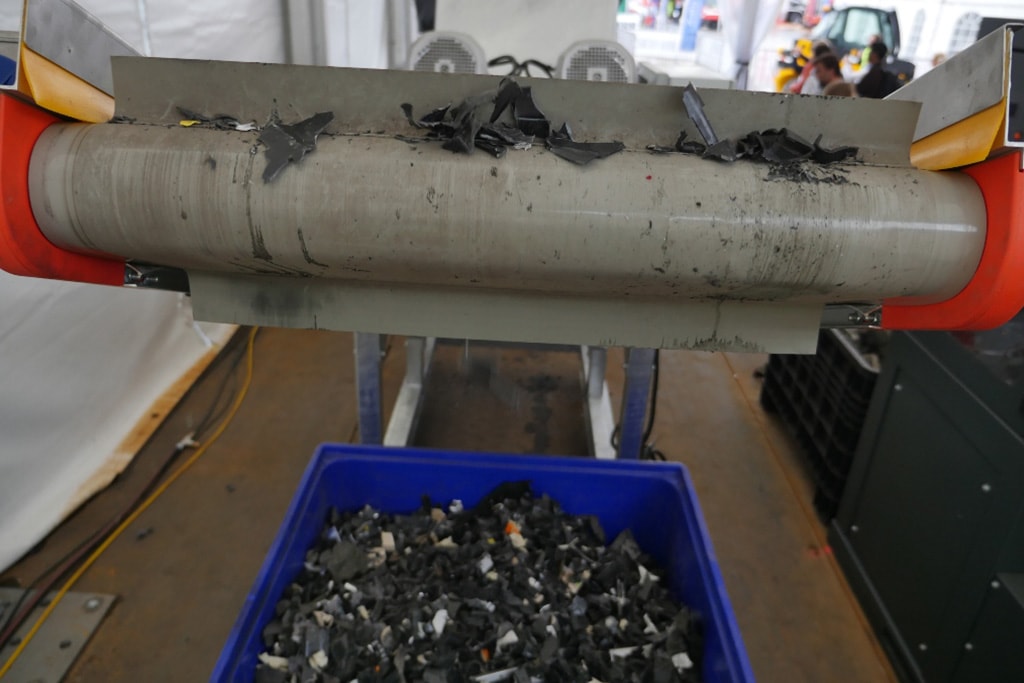
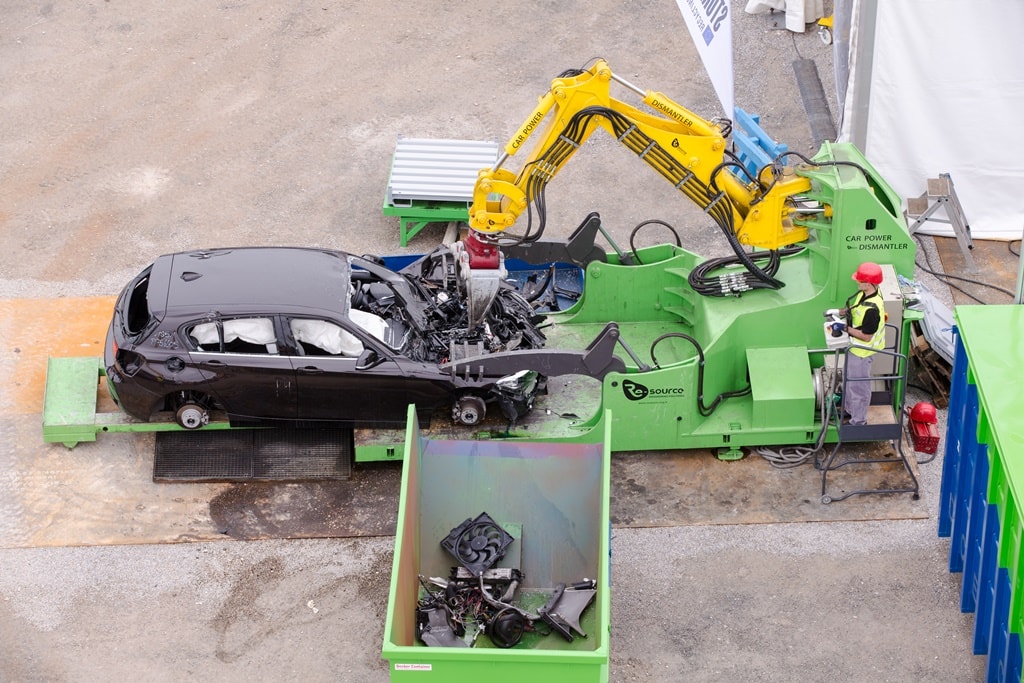

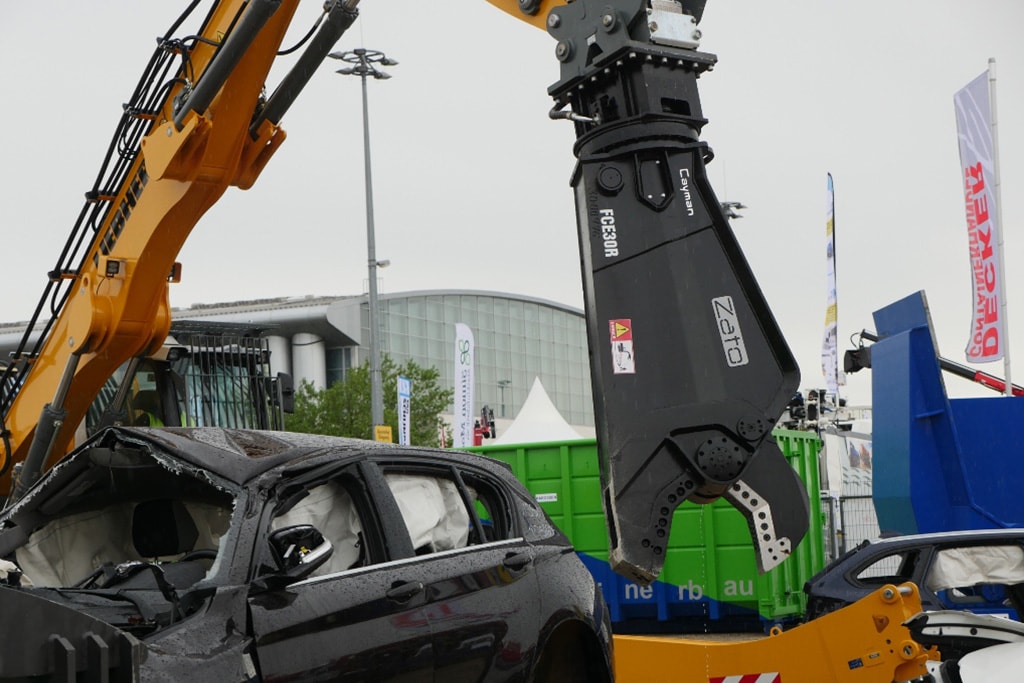
At the fifth station you can see the reprocessing. It includes a parts-cleaning table of Re-source, the T-REC XXL of SEDA that makes light work of tyre and wheel separation, the neutralization of extracted airbags with the SEDA ANC, the chopping of electric motors with the E-Motorchop of Stokkermill, the engine breaker of Roter, plastic shredders by Re-source as well as the separation of cables and metals using the CableShredder of Stokkermill. Additional machinery of the reprocessing involves the car power dismantler of Re-source and the mobile scrap shear of Zato, which fits perfectly together with the LH30M Industry Litronic of LIEBHERR. Also the telescopic handlers TL436-7 Litronic of LIEBHERR is used.
06 Compression
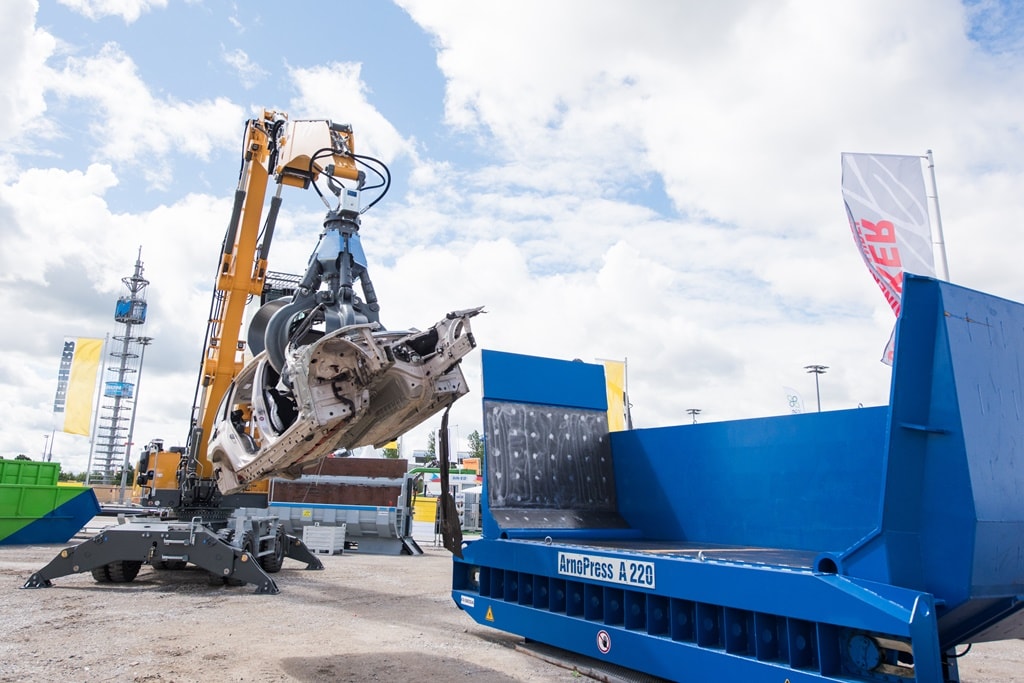
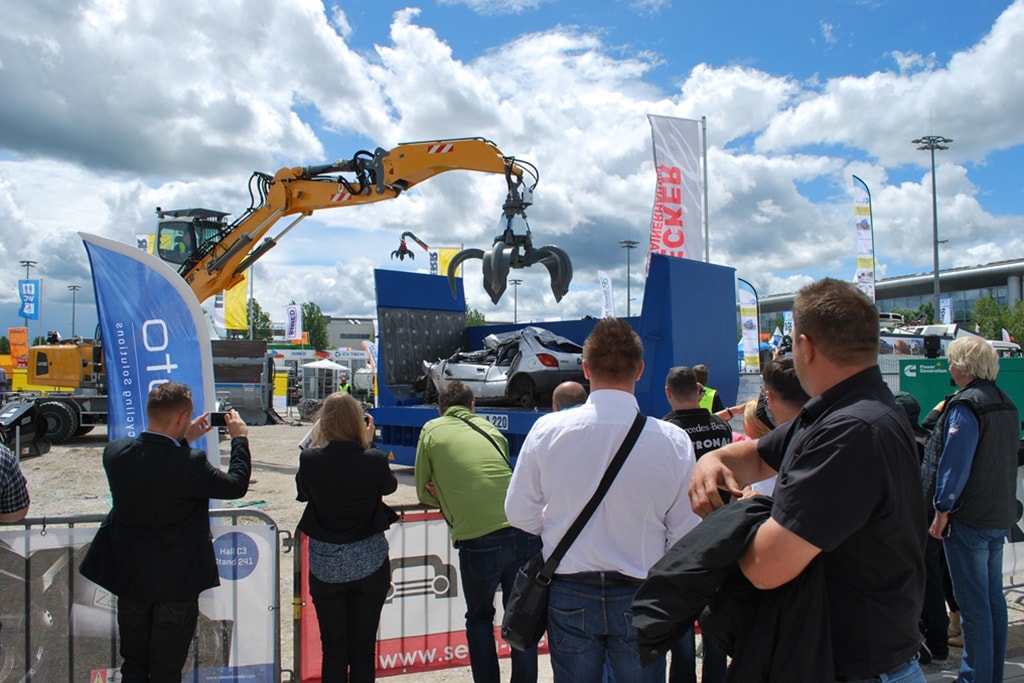
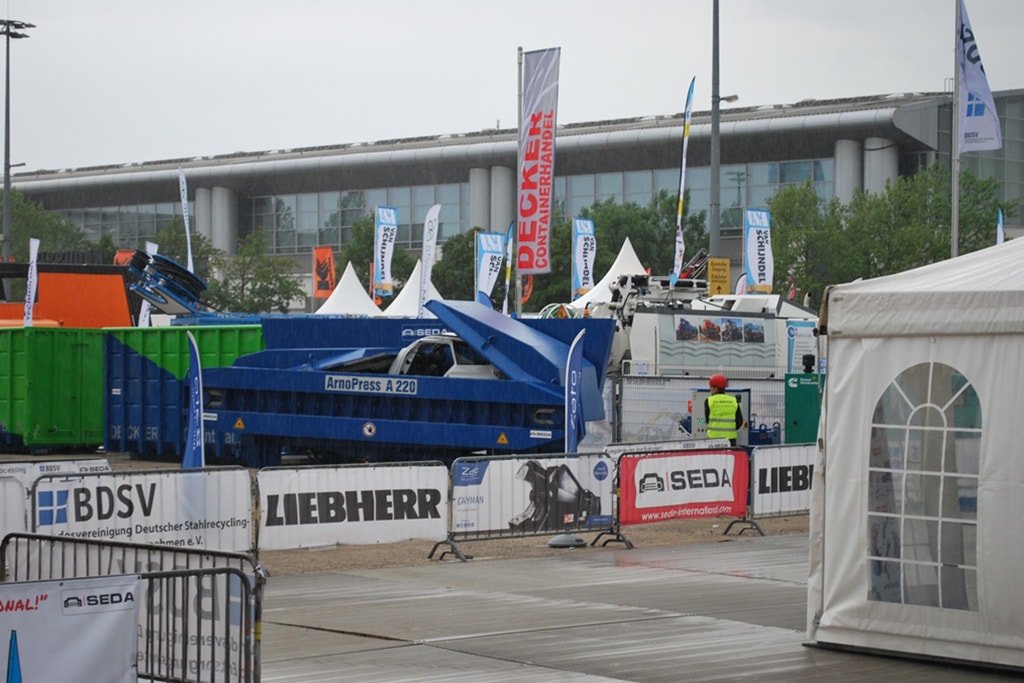
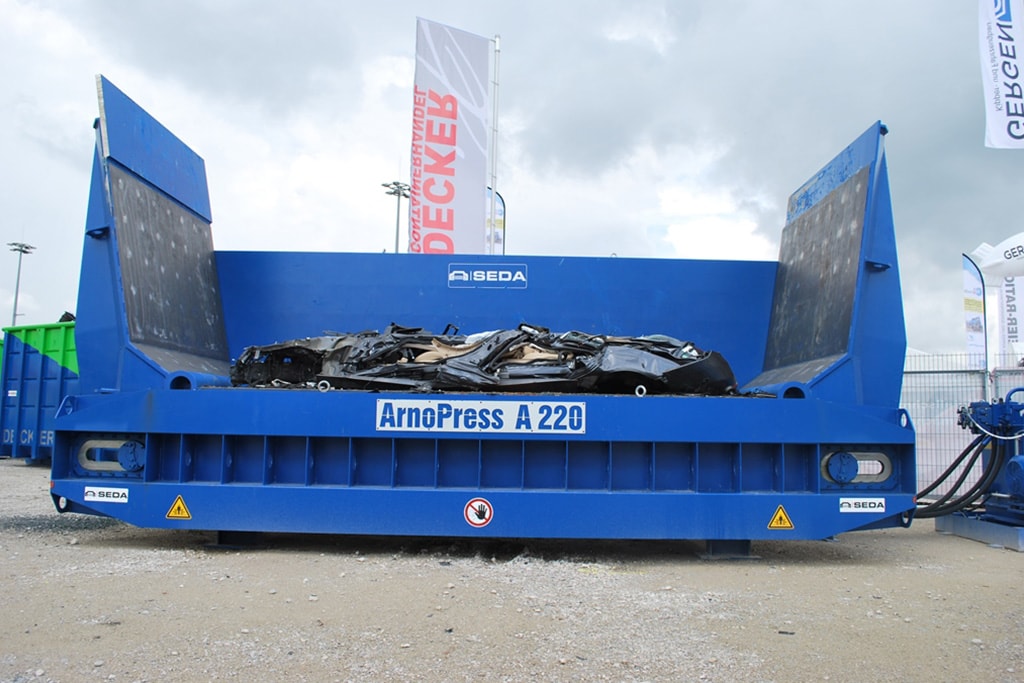
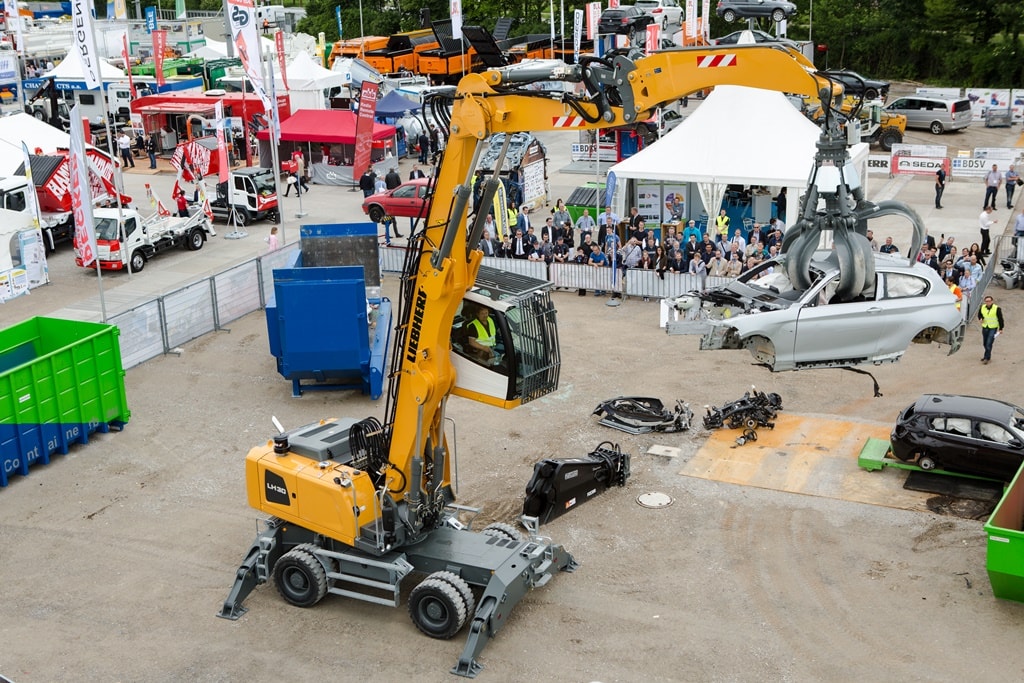
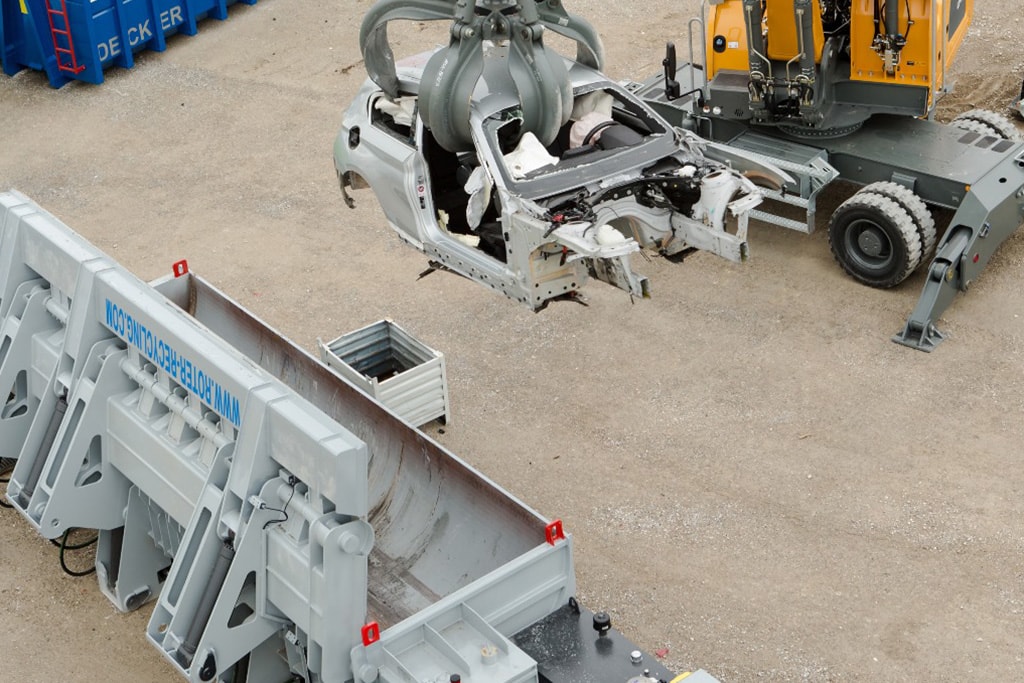
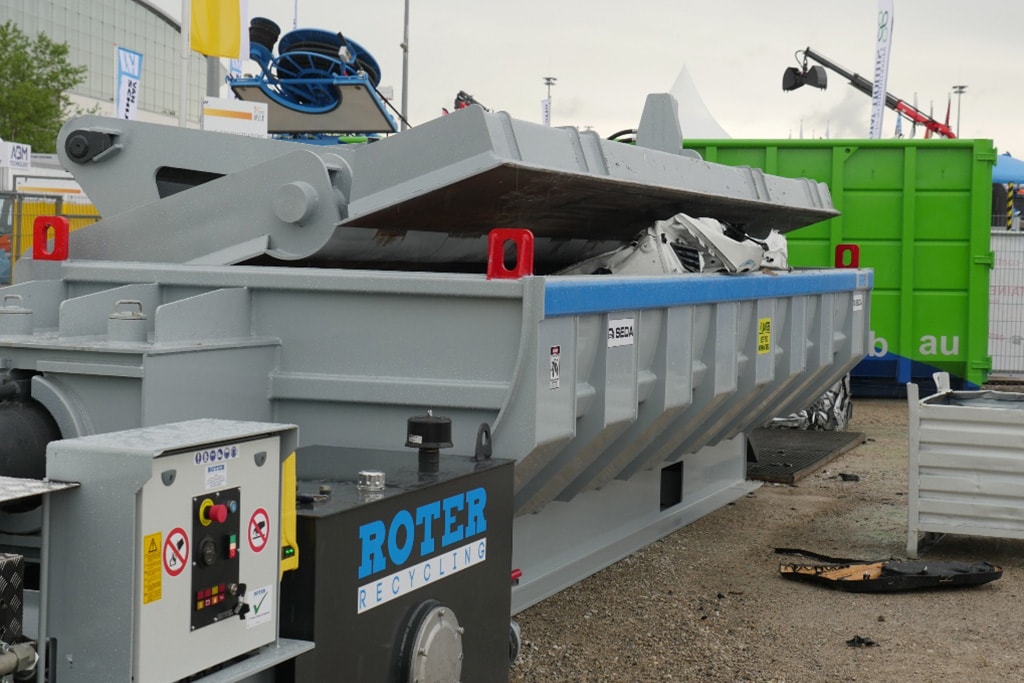
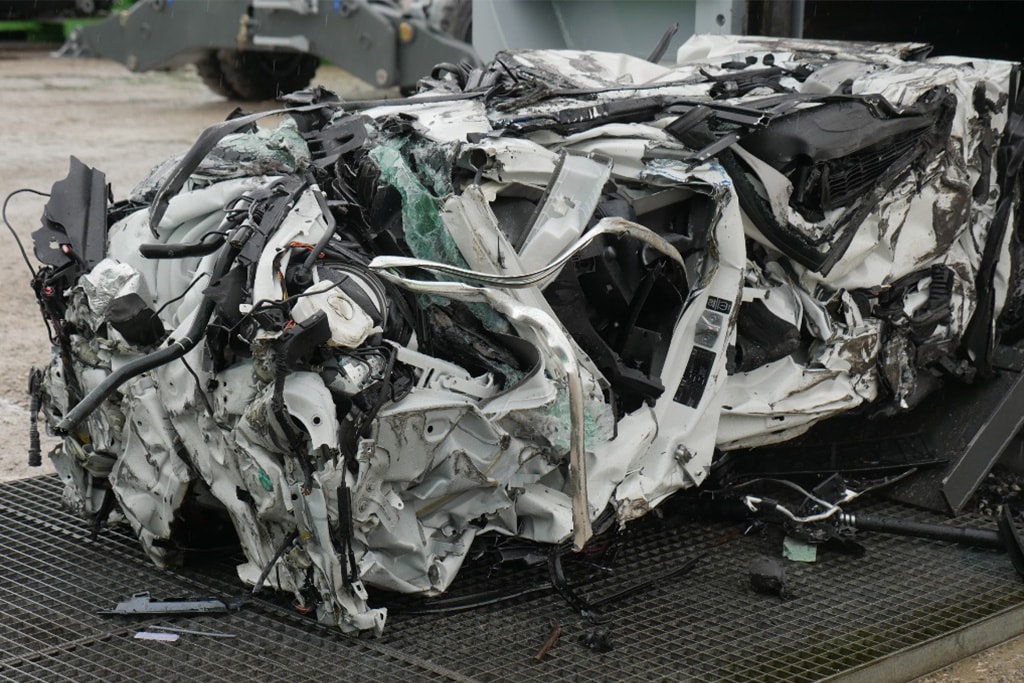
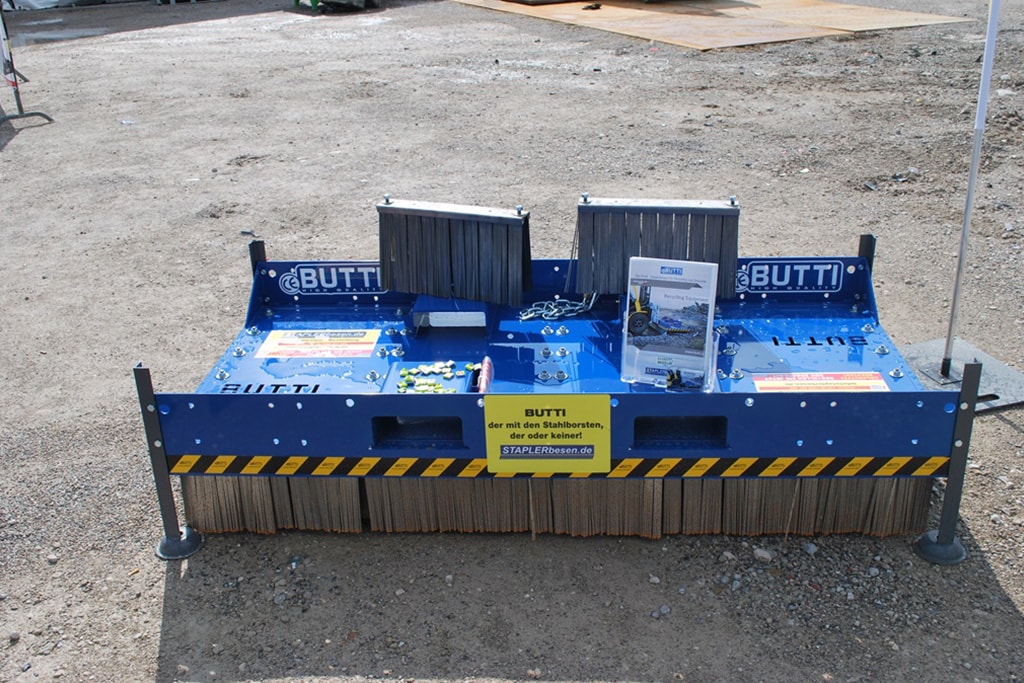
The compression of car bodies completes the recycling process shown at the IFAT 2016. There are two options. On the one hand the SEDA CarFlattener, that squeezes wrecked cars to a length of 3.8 m and a height of 35 cm in one operation with a press force of 110 tons. It ensures a flat car body. Secondly, the CarPress of Roter ejects scrap packages. The compressed bales have a size of 800 x 1200 mm.
References
List of exhibitors and partners
- BDSV
- SEDA-Umwelttechnik GmbH
- KUMAsoft GmbH
- LIEBHERR
- BMW
- Frimberger GmbH
- Zato Recycling Solutions
- Decker Reinhard Containerhandel
- JCB Deutschland GmbH
- Grosse Lagertechnik & Stahlbau
- ATM Recycling Systems
- STAPLERbesen.de
- Roter Recycling
- Re-source Engineering Solutions
- Stokkermill Recycling Machinery
- Mercedes Benz
Links
Articles:
- Final report IFAT.de
- fairmessage.de
Pictures:
Videos: